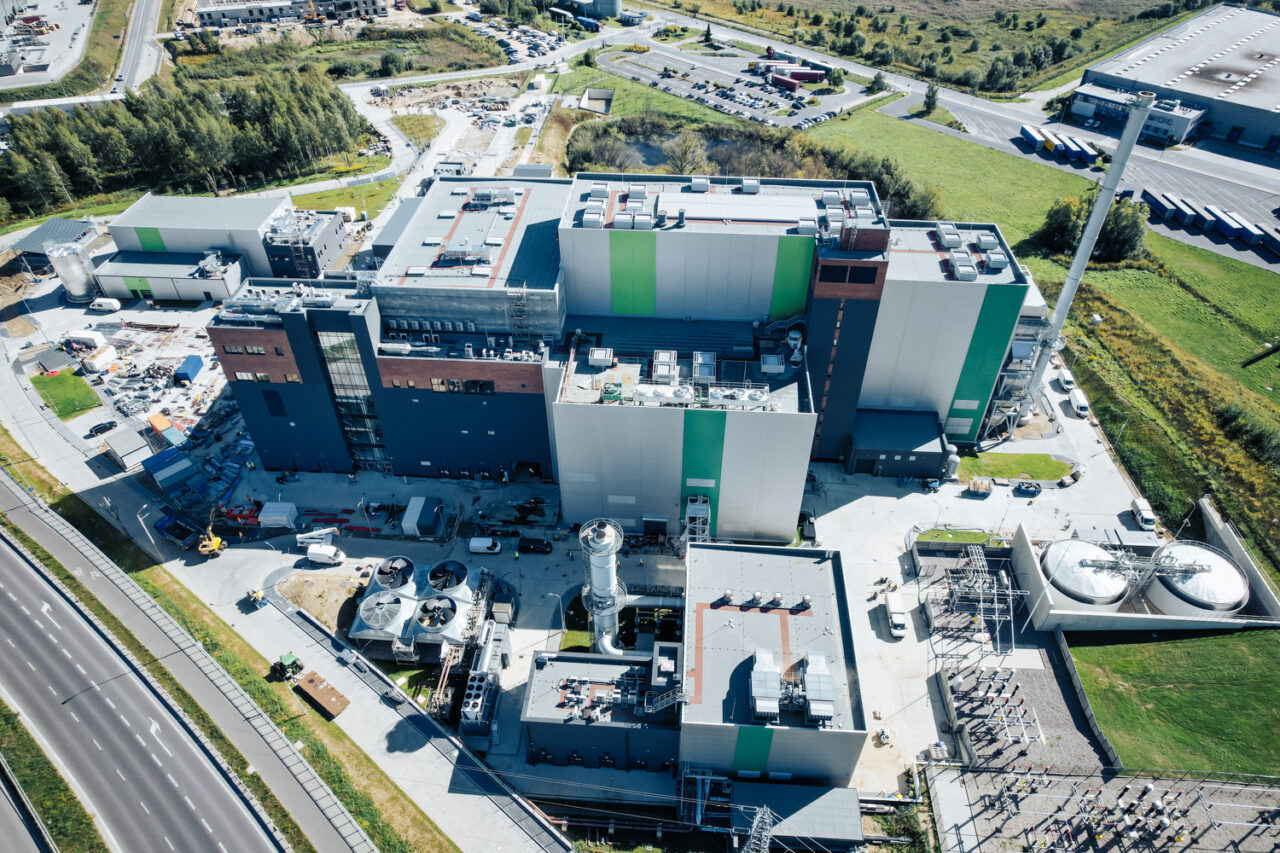
Waste incineration plant in
“Olsztyn”
The city of Olsztyn was faced with the challenge of finding an environmentally friendly and efficient solution for the disposal of over 100,000 tonnes of residual waste every year. The aim was to construct a waste incineration plant that would not only thermally utilise residual waste and reduce the need for landfill space, but also contribute to meeting the region’s district heating requirements. The thermal utilisation is expected to cover around 30% of Olsztyn’s district heating requirements, which will help to replace fossil fuels.
In addition, the plant will also generate a considerable amount of electrical energy and feed it into the public grid.
NOPA was commissioned to develop and provide the valve technology for the plant in collaboration with various project partners. The plant had to be designed to function reliably at vapour temperatures of up to 450 °C and pressures of up to 40 bar. Particular attention was paid to standardising the valves to reduce diversity and make maintenance and spare parts supply more efficient.
Client: Doosan Lentjes GmbH
Operating company: Dobra Energia Dla Olsztyna Sp. z o.o.
Period: 2021 – 2024
Location: Olsztyn, Polen
Special features:
- Fully autonomous waste disposal system
- Generation of approx. 30% of the region’s district heating requirements
- Significant amounts of electrical energy are fed into the public grid
Contact person NOPA:
Robert Schmidt
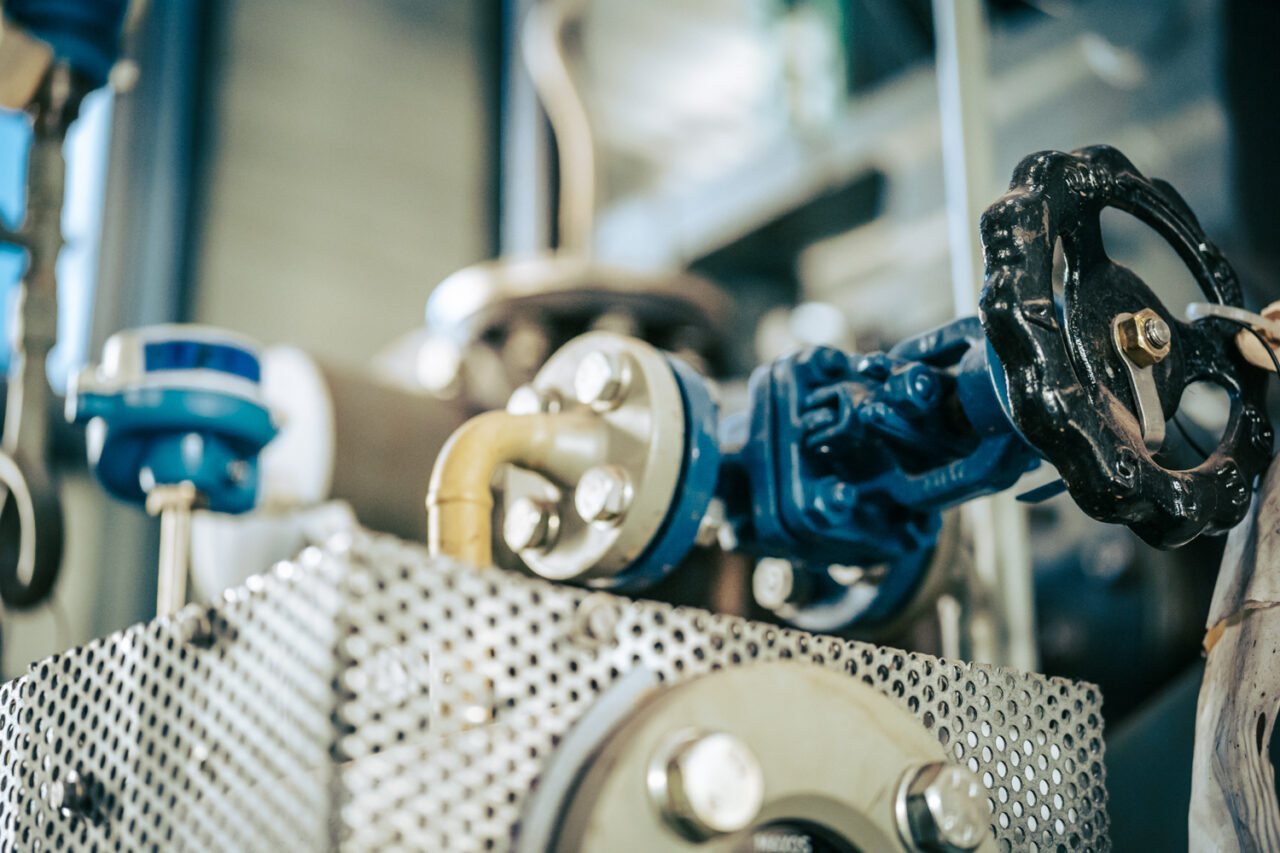
Early integration for efficient valve standardization
Planning
The pipework planning for the waste incineration plant was carried out by Enertech Energie und Technik GmbH, a long-standing partner of NOPA. The early involvement of NOPA in the planning phase made it possible to adapt the pipework layout precisely to the requirements of the valve technology.
A common goal was to standardise the valves as far as possible in order to optimise maintenance costs and the stocking of spare parts. This standardisation reduces operating costs in the long term and ensures greater availability of the required components.
In close co-operation with the general contractor for the project Doosan Lentjes GmbH and the operating company Dobra Energia Dla Olsztyna Sp. z o.o., the valve design was adapted precisely to the operating conditions.
Complete equipment with tailor-made fitting technology
Implementation
In the implementation of the valve technology, NOPA convinced with its high-quality offer as a supplier for the main valve contingent and thus became almost the full range supplier for the waste incineration plant in Olsztyn. This included control valves, shut-off valves, safety valves and other special valves suitable for use in waste incineration plants. The valves supplied were designed with a view to reliability, durability and resistance to high temperatures and pressures and, in some cases, aggressive media.
It goes without saying that only valves that have undergone functional and leak tests and can withstand thermal loads of up to 450 °C and pressures of up to 40 bar were used.
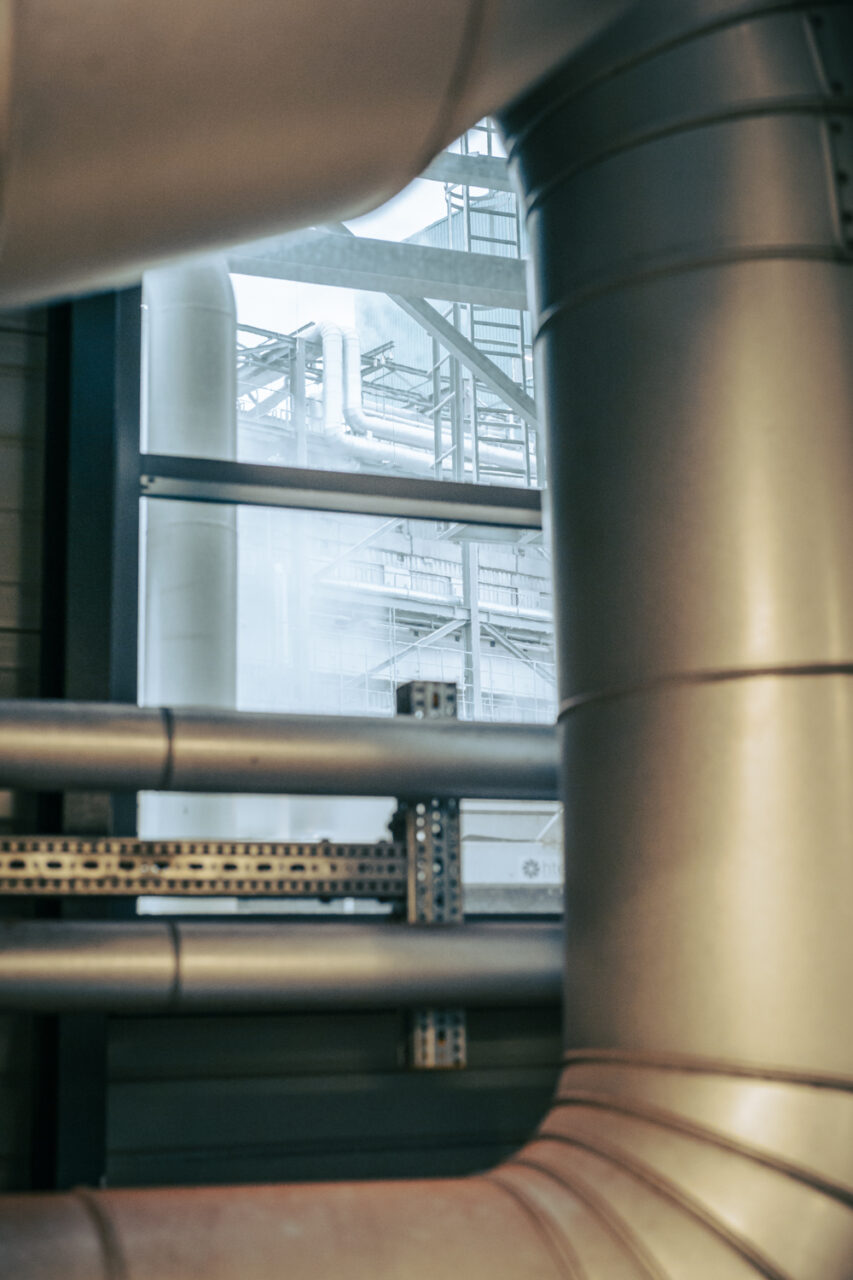
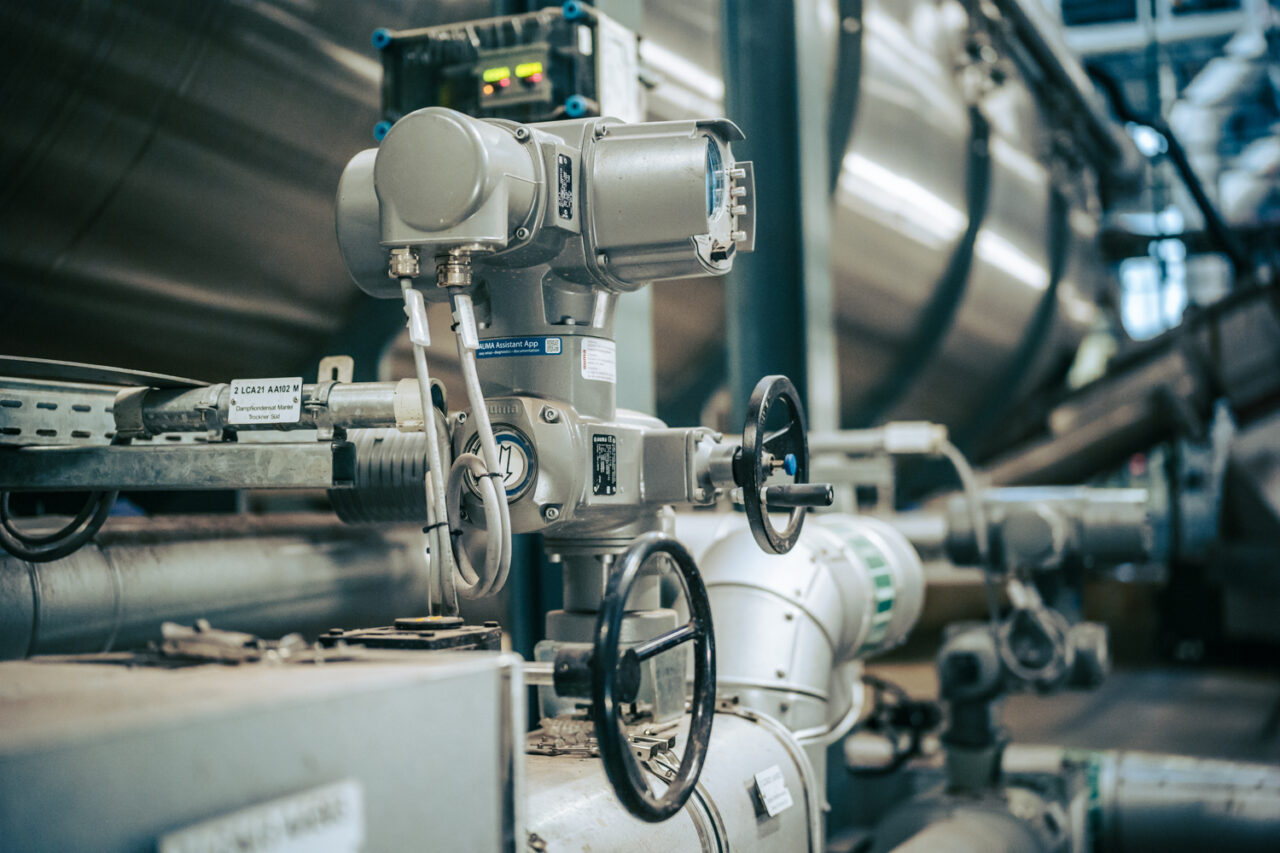
Successful commissioning with sustainable energy generation
Result
The Olsztyn waste incineration plant was successfully put into operation and fulfils its tasks in full. It makes a significant contribution to the thermal utilisation of over 100,000 tonnes of residual waste every year, thereby reducing the need for landfill space and the release of climate-damaging methane.
In addition, the plant covers around 30% of the Olsztyn region’s district heating requirements and feeds considerable amounts of electrical energy into the public grid, thereby replacing fossil fuels on a large scale.
Thanks to the close cooperation with the project partners Enertech Energie und Technik GmbH, Doosan Lentjes GmbH and Dobra Energia Dla Olsztyna Sp. z o.o., NOPA was able to deliver a made-to-measure and efficient valve solution. The standardisation of the valves used has led to a considerable reduction in the variety of types, which not only simplifies spare parts management and maintenance, but also significantly reduces the operating costs of the plant.
This project demonstrates NOPA’s ability to deliver and successfully implement solutions even under extreme conditions. The plant is an important part of the regional energy supply and makes a significant contribution to a reduction in the use of fossil fuels.