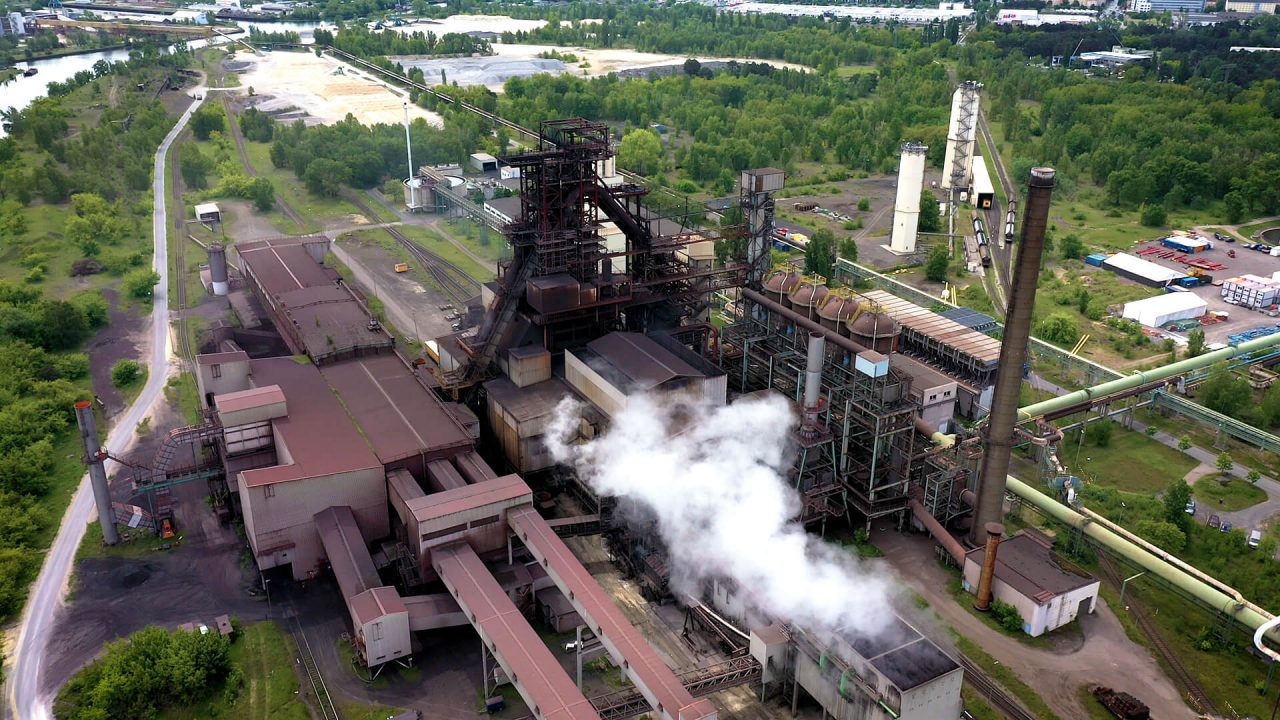
ArcelorMittal Steel group
“Blast furnace natural gas injection”
Industry accounts for almost one fifth of global co2 emissions. Reducing the co2 footprint should be a concern for every company, at least since the introduction of co2 pricing. The arcelormittal steel group is tackling the issue as part of its sustainability strategy to reduce its co2 emissions. And through a joint project with nopa, it is now saving 163,000 tons of co2 emissions a year.
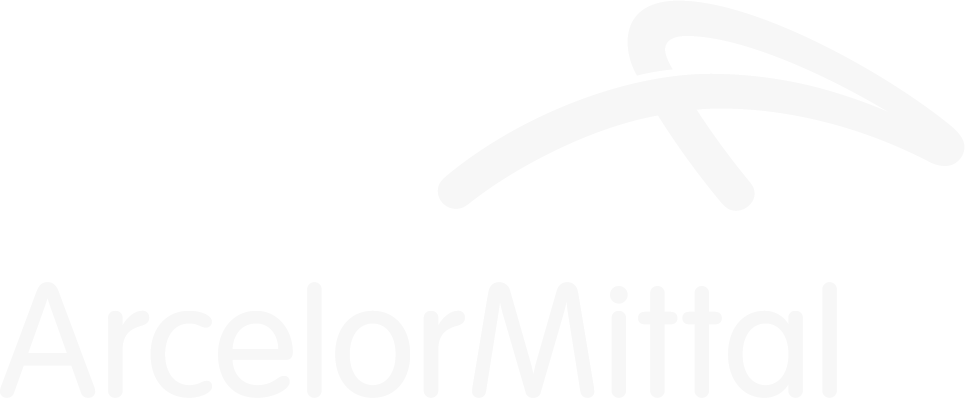
Client: ArcelorMittal
Project period: 2021
Location: Eisenhüttenstadt
Special features:
- Project planning and design by NOPA
- Replacement of lignite by natural gas
- Savings in co2 emissions
- Increased plant availability
Contact person NOPA:
Robert Mytzka
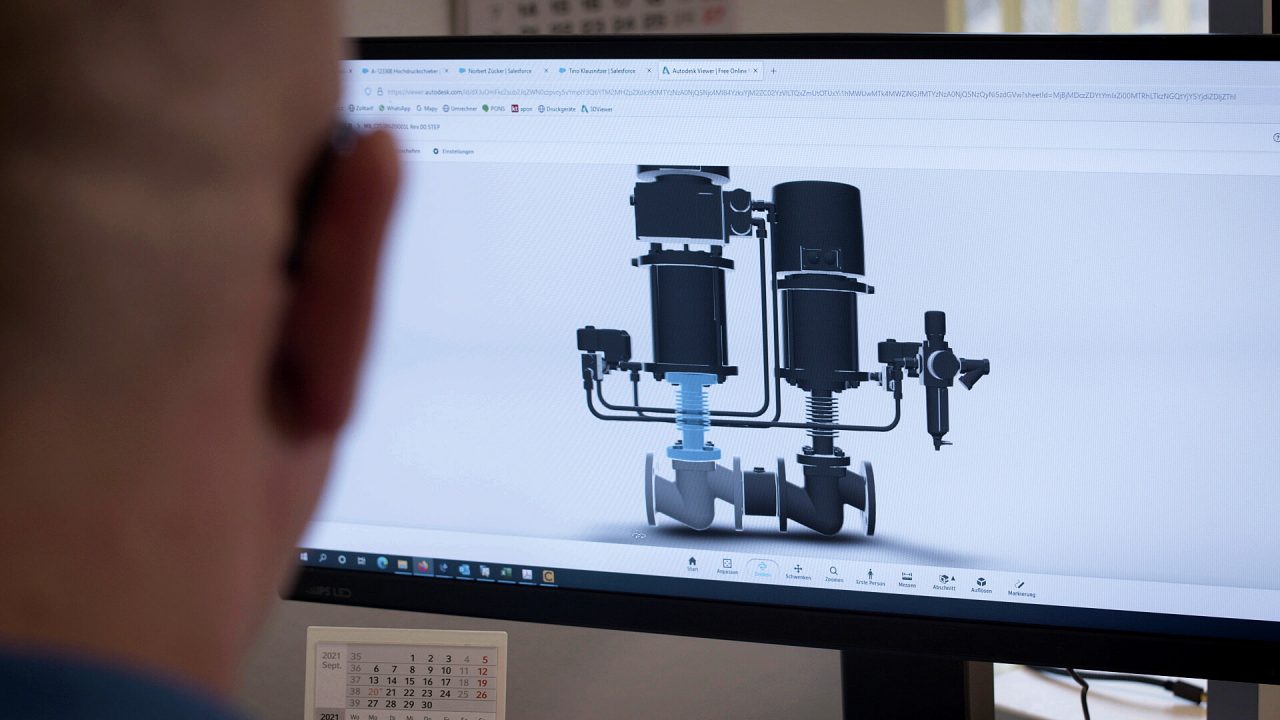
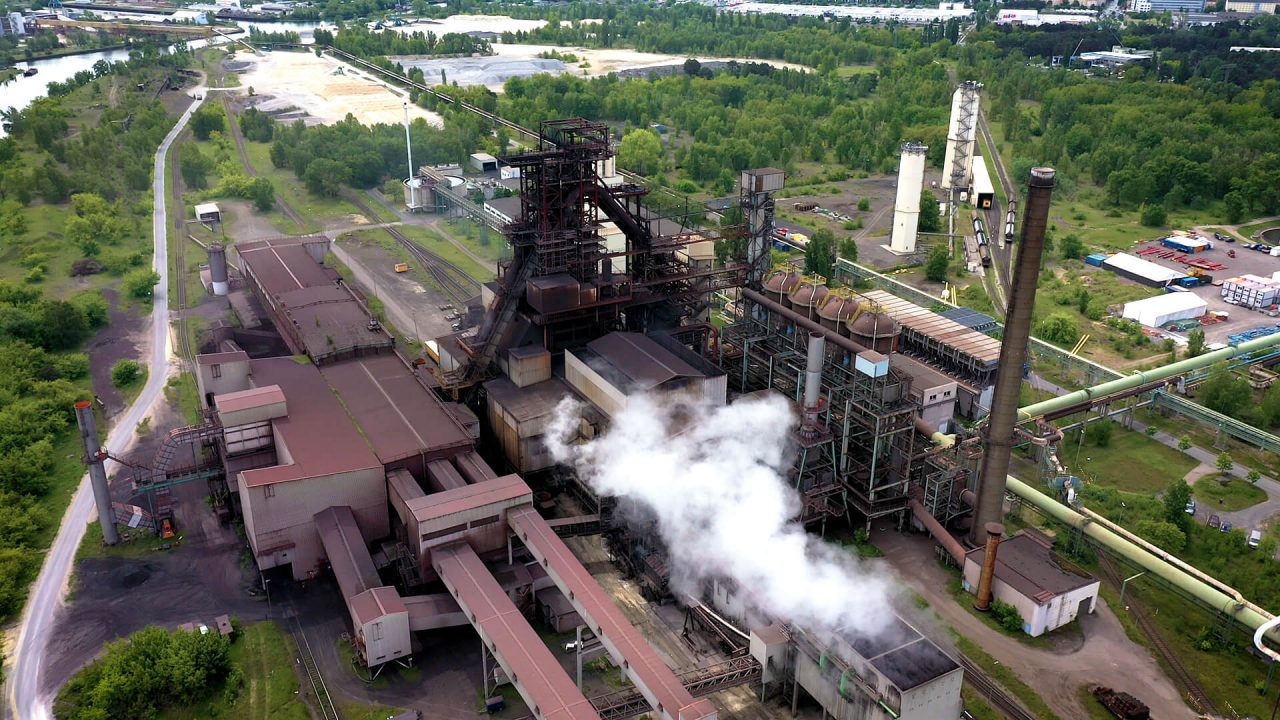
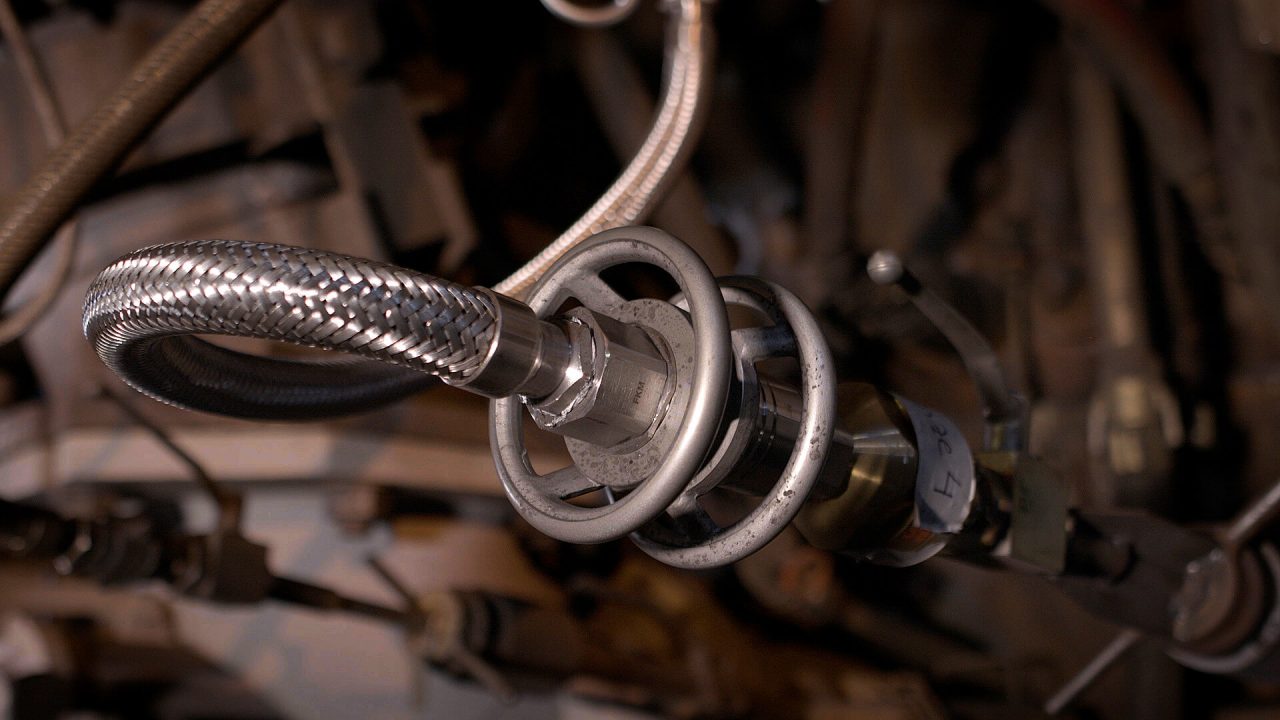
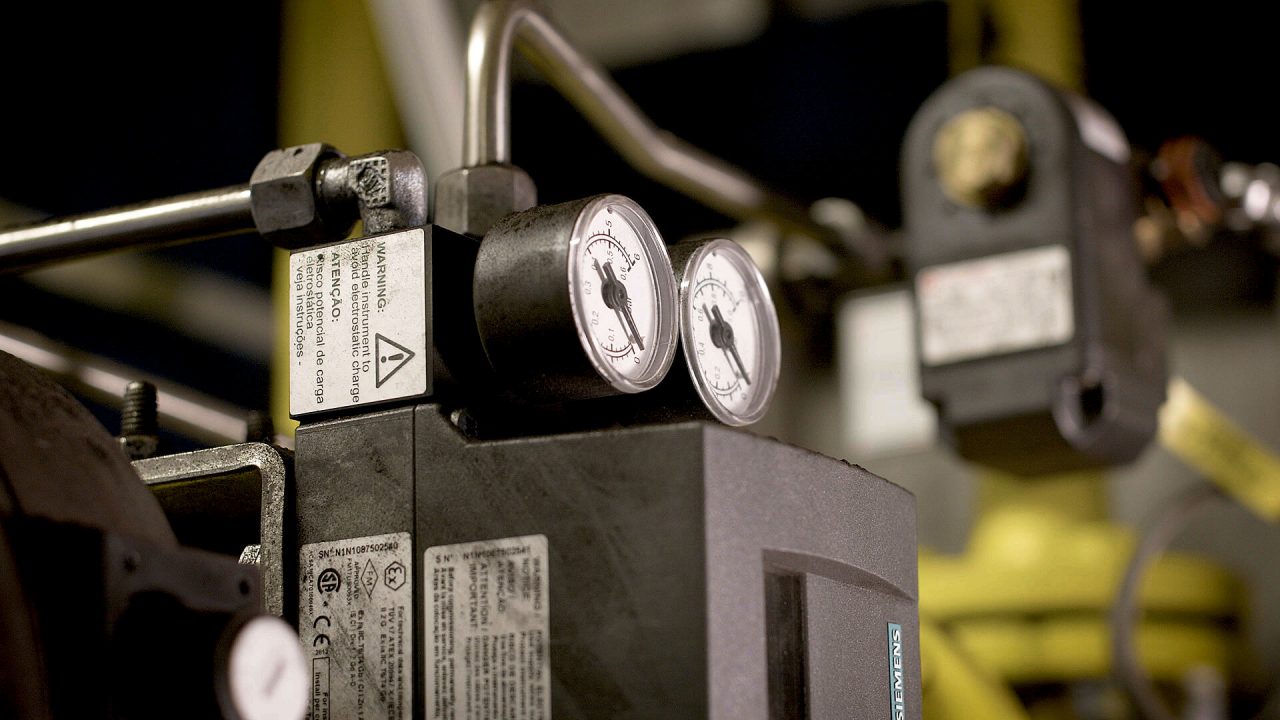
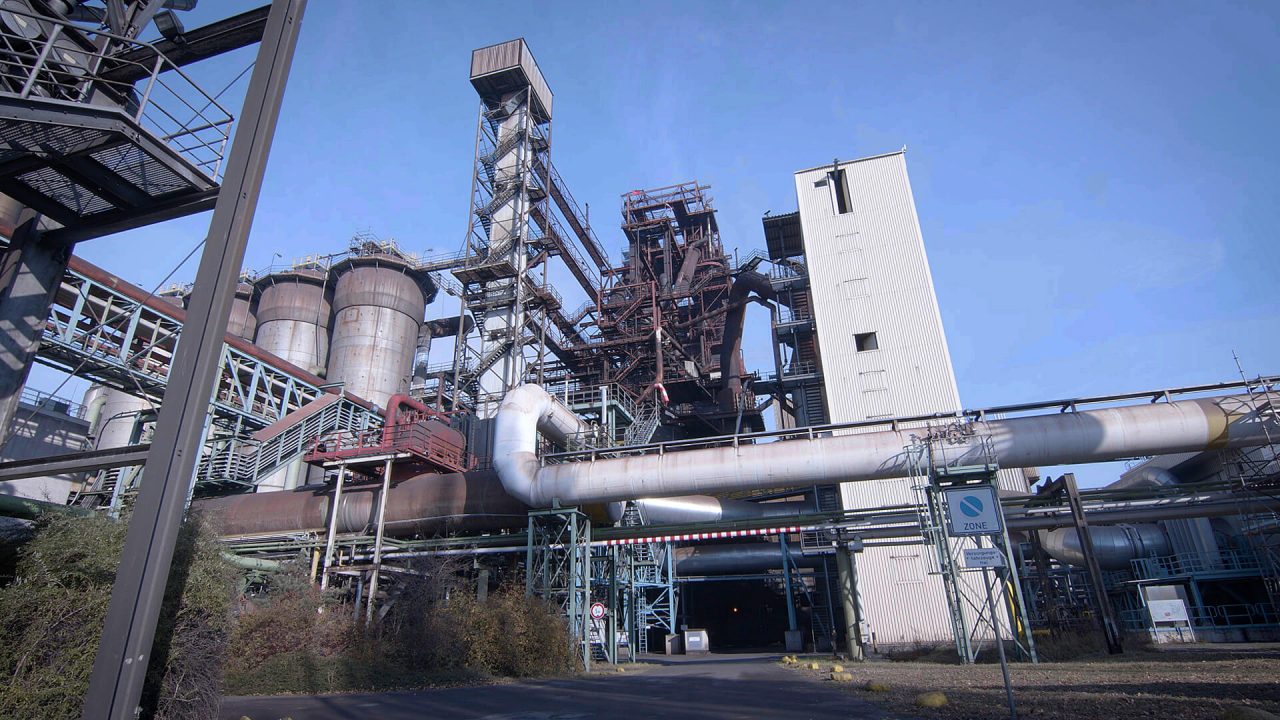
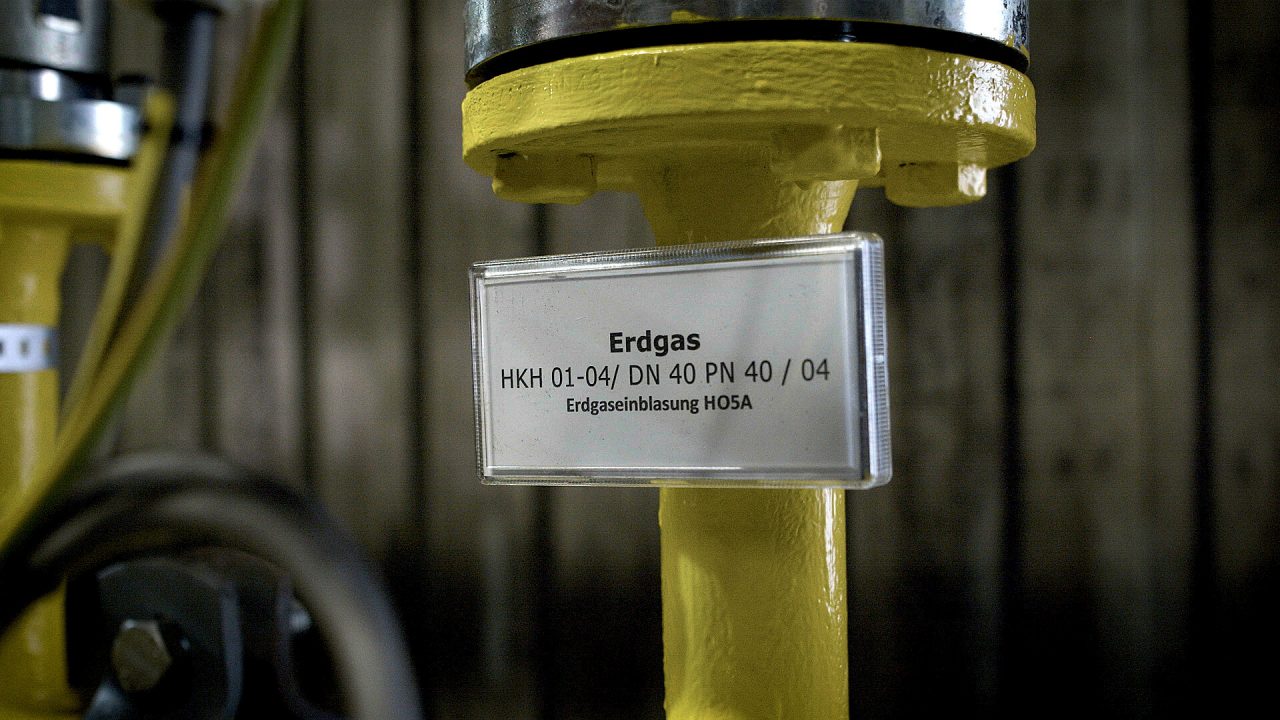
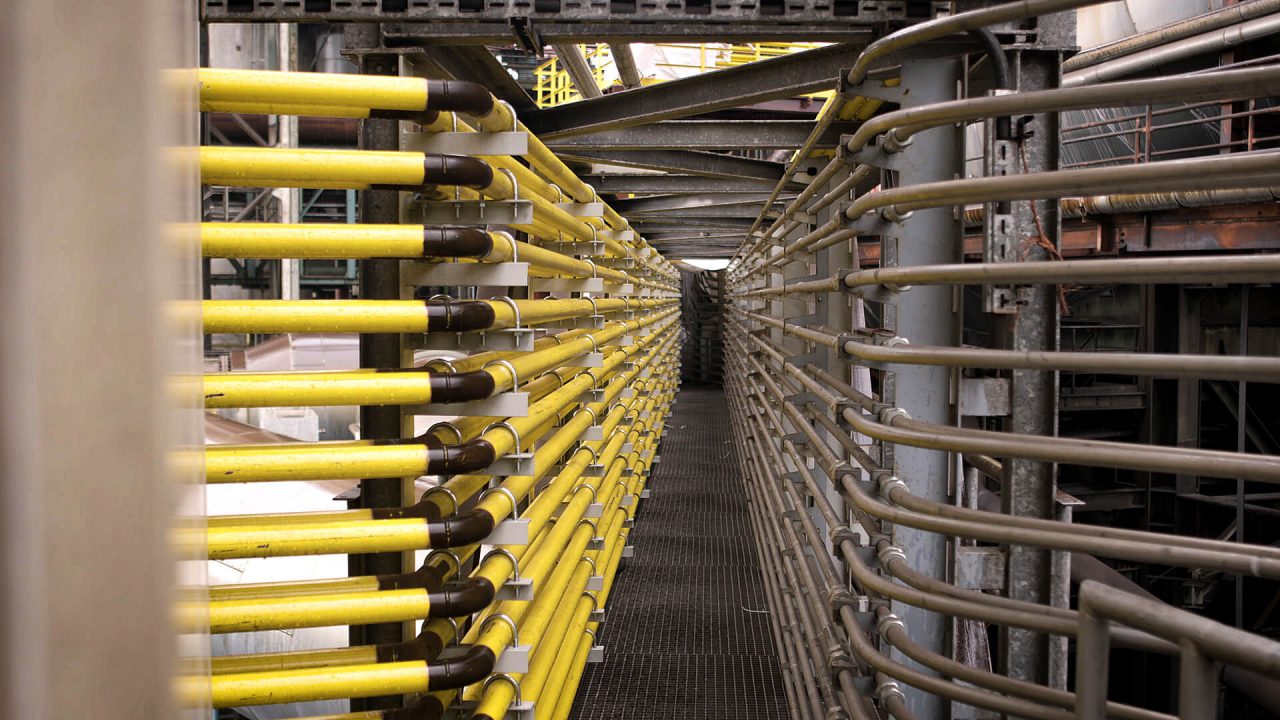
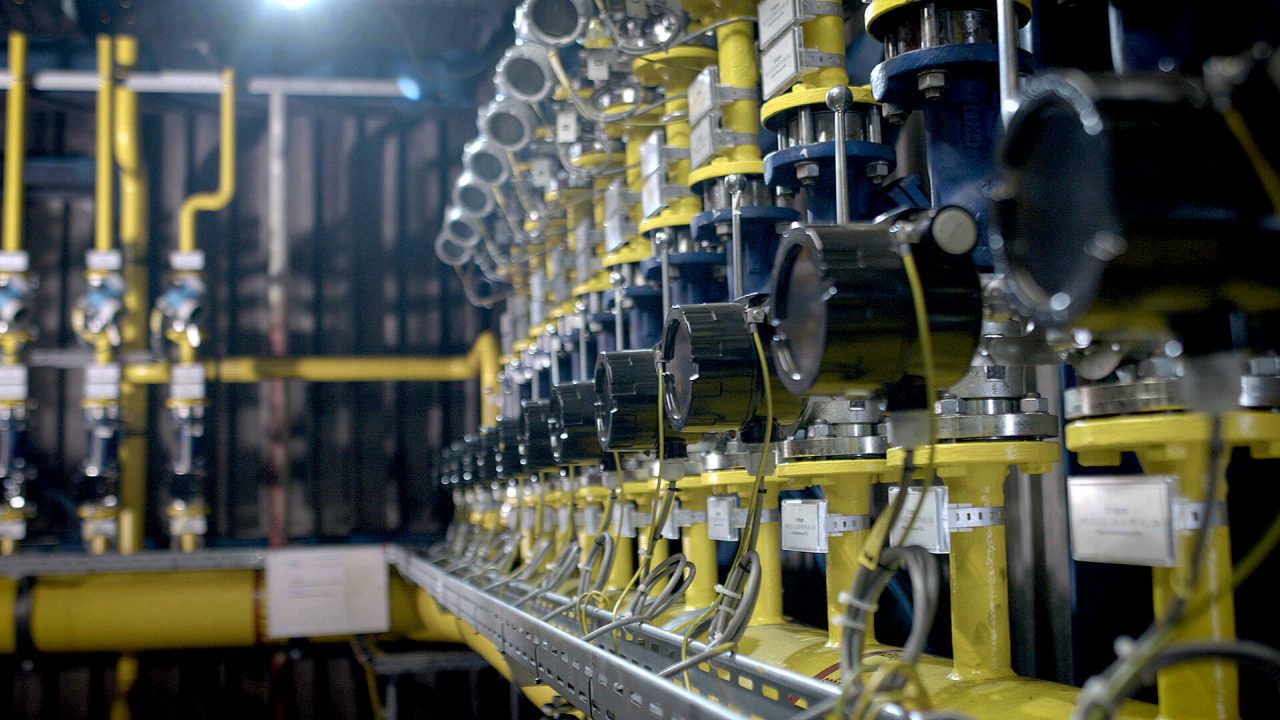
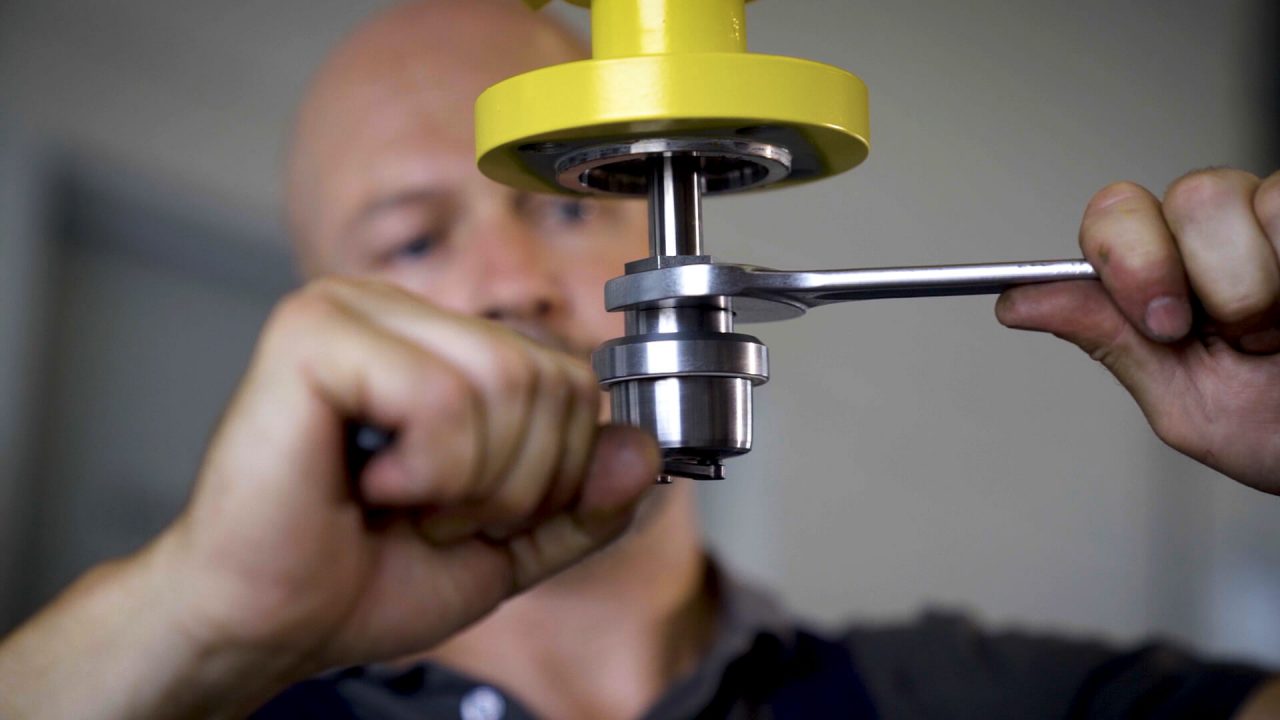
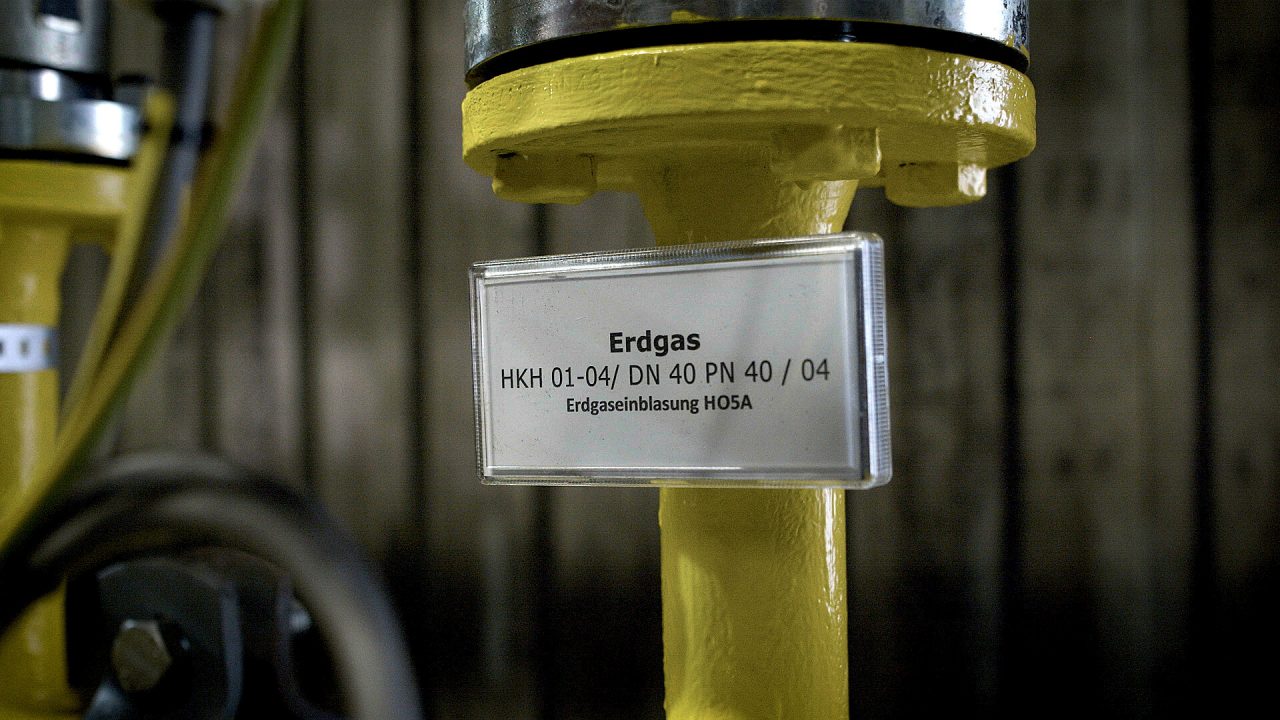
CO2 savings
Injection of natural gas into a blast furnace
Together with NOPA, ArcelorMittal tackled the reduction of its co2 footprint. The aim of the project was to install a natural gas injection system for the ho5a blast furnace, via which a metered amount of natural gas can be injected into the blast furnace.
NOPA supported ArcelorMittal during the project planning phase, optimized the planned fittings and contributed to enormous cost savings thanks to a reduction in pipe diameters and the number of fittings. At the same time, our service technicians were able to realize the targeted co2 savings with the rebuild.
Replacement of coal by natural gas
Multi-stage plan for co2 reduction
The HO5A is a modern blast furnace. For every ton of pig iron produced, it releases around 1.6 tons of CO2 emissions into the atmosphere. This results from the blast furnace process, which uses carbon and carbon monoxide to reduce the iron ore. To produce the desired product, the HO5A currently blows in around 230 kg/thm of coal, 60 percent of which is hard coal and 40 percent lignite.
Due to existing restrictions and environmental regulations, it is necessary to reduce the blast furnace’s CO2 emissions. For this purpose, ArcelorMittal has created a multi-stage plan. The first stage – replacing lignite with natural gas – was implemented by NOPA 2021 together with the company. As a result, a significant amount of co2 can now be saved each year.
The key data of the project at a glance:
- Injection of up to 20,000 m³ i.N. natural gas at a pressure of 10to 16bar
- Transport of the natural gas to the distribution station and injection via 26 lances
- Control of the system via plc control for metered feeding
- Control range of the flow meter (MFC) between 30 nm³/h and 900 nm³/h
- Shutdown of individual lances at minimum injection rate
- Climatic conditions: altitude above sea level approx. 45 meters, -25°c to +45°c assumed air temperature
- Maximum availability of the plant
From project planning to realization
Consulting, calculation and optimization by NOPA
The process to be created involves piping the natural gas from the upstream supplier’s injection point to a gas pressure control and metering system, where it is brought to the pressure of 10 to 16 bar required for the blast furnace process. A pipeline then conveys the natural gas to the distribution station, from where it is divided into 26 lances and injected into the ho5a blast furnace via a pipe bridge. NOPA supported the project during the project planning phase.
The focus was on two areas:
- Pipe cross-sections: NOPA calculated the required piping cross sections to implement the project. By calculating the required flow rates and pressure losses, some pipelines could be made smaller. This saved ArcelorMittal material and costs on the one hand, but also valuable space on the other.
- Optimizing the use of valves: our engineers designed the valves responsible for regulating the injection and the shut-off. The previously planned three valves (double shut-off function, control function) were replaced by a single hybrid valve that combines three functions: a double shut-off and the control function. This made it possible to save 26 valves.
NOPA accompanied the entire project from consulting during the project phase, to later optimization due to changes made in the meantime, to delivery of the valves and renewed optimization during the implementation phase.
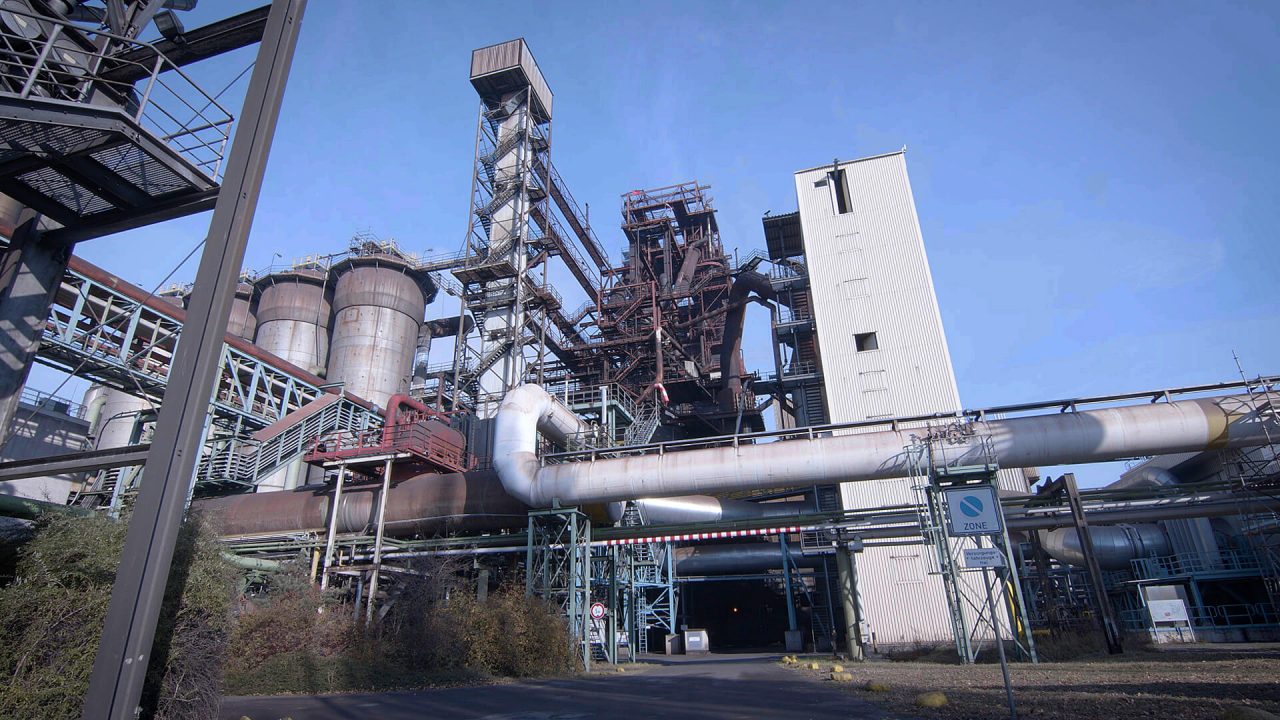
Benefits of the project
Thanks to retrofitting 163,000 tons of co2 saved per year
The project to inject natural gas into the ho5a blast furnace has brought ArcelorMittal a big step closer to its major goal of improving the company’s carbon footprint. As a result, the steel mill is reaping the benefits:
- Savings of 163,000 tons of co2 per year
- Higher plant availability
- Cost savings due to lower material consumption
- More favorable space conditions