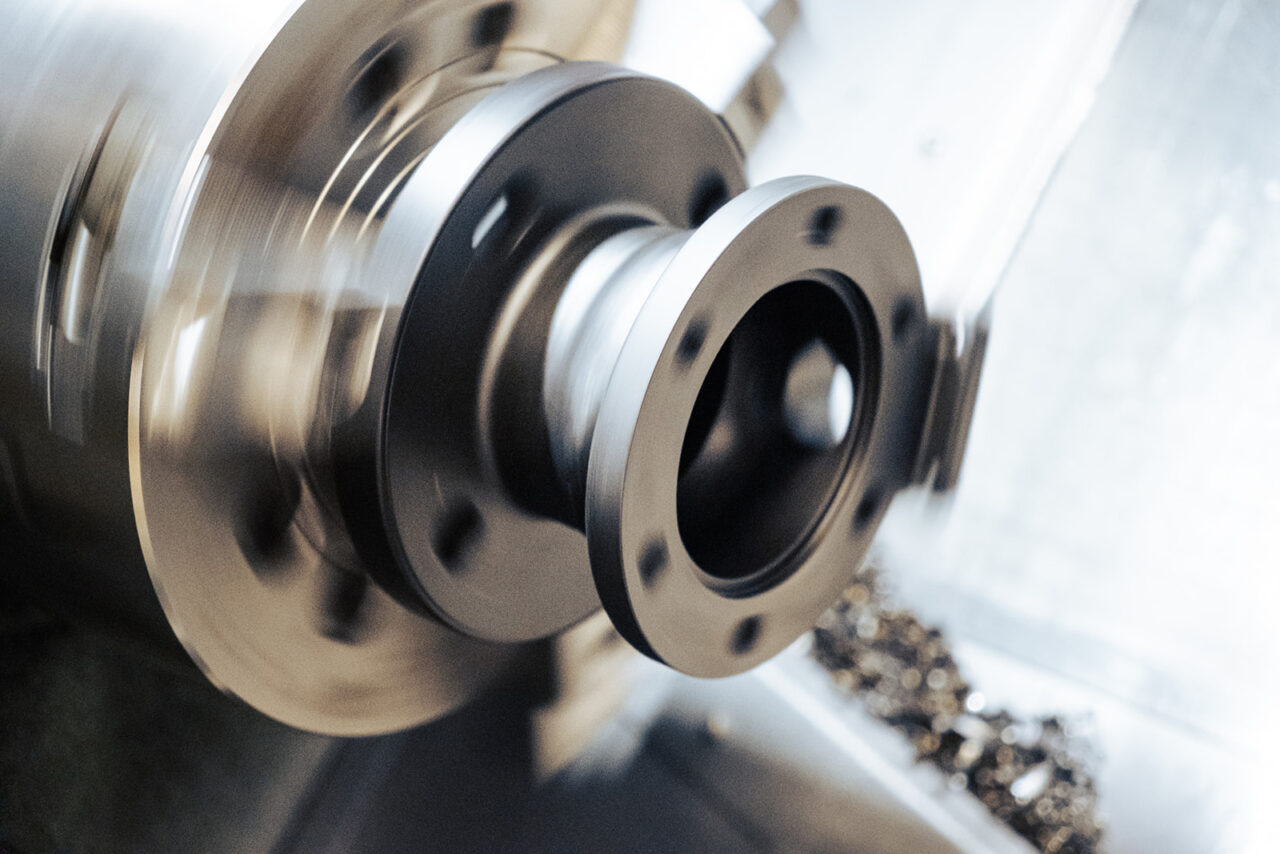
The use of hydrogen in the energy transition
The challenge
In the course of the energy transition, hydrogen will play a decisive role as an energy storage medium. Electrolysis splits water into hydrogen and oxygen. A widely used process for this is alkaline electrolysis (AEL), in which water is mixed with potassium hydroxide (KOH) to form an alkaline solution. Splitting then takes place at nickel-based electrodes, which are separated from each other by a gas-impermeable membrane.
The technical challenge in this process is that common metallic valve materials are not resistant to potassium hydroxide. At the same time, however, resistant plastic-based materials cannot withstand the high pressures and temperatures. NOPA was commissioned to develop valves that can withstand the extreme conditions of alkaline electrolysis and ensure safe use.
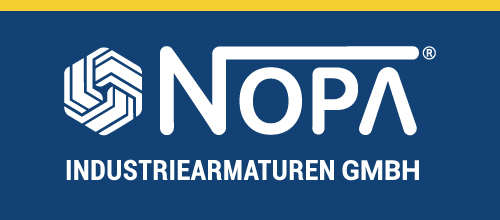
Project: NOPA Chem valves, for potassium hydroxide
Client: McPhy Energy GmbH
Period: 2022 – ongoing
Special features:
- Nickel coating for potassium hydroxide resistance
- NOPA’s transformation into a fittings manufacturer
Contact person NOPA:
Robert Schmidt
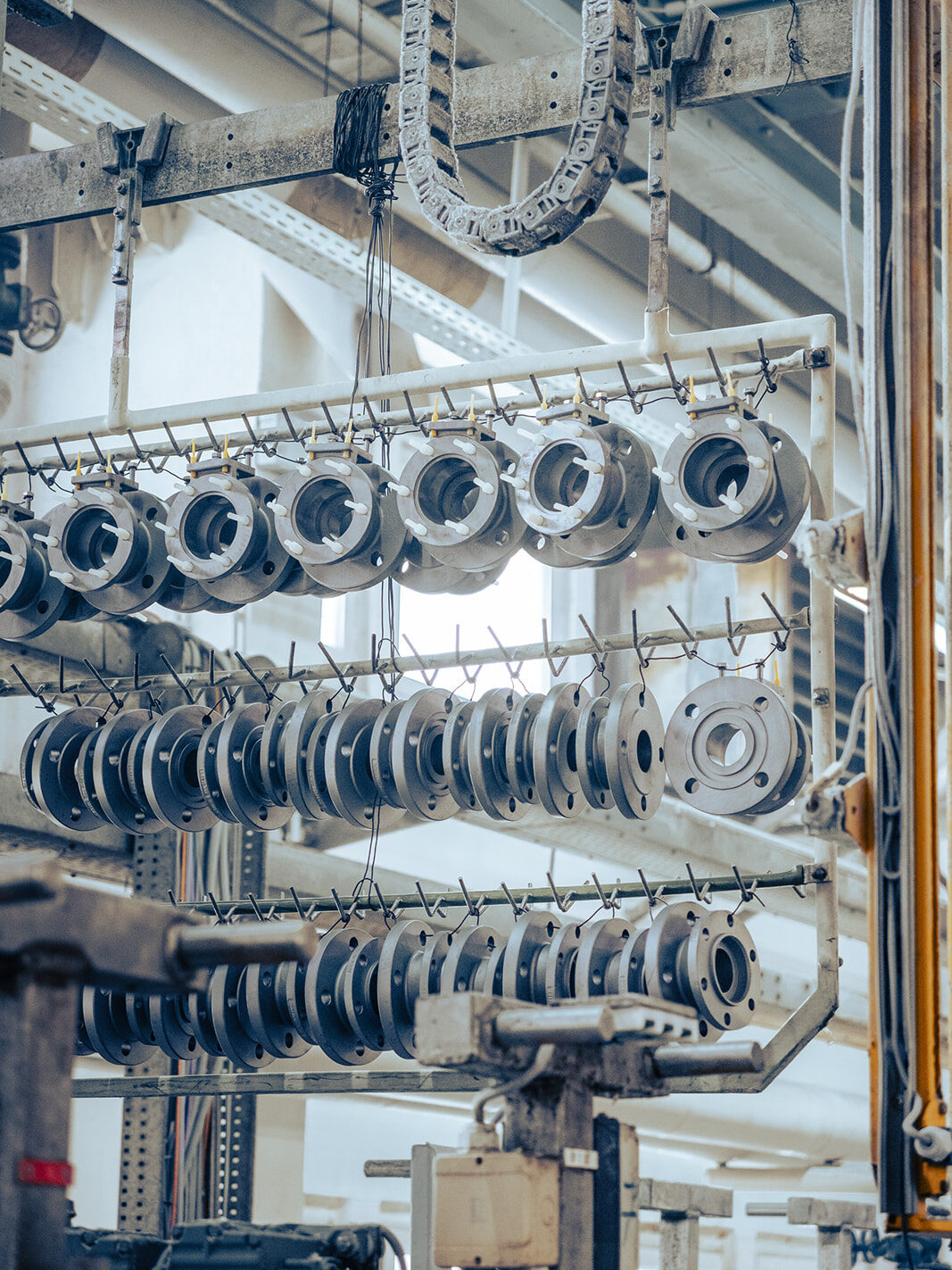
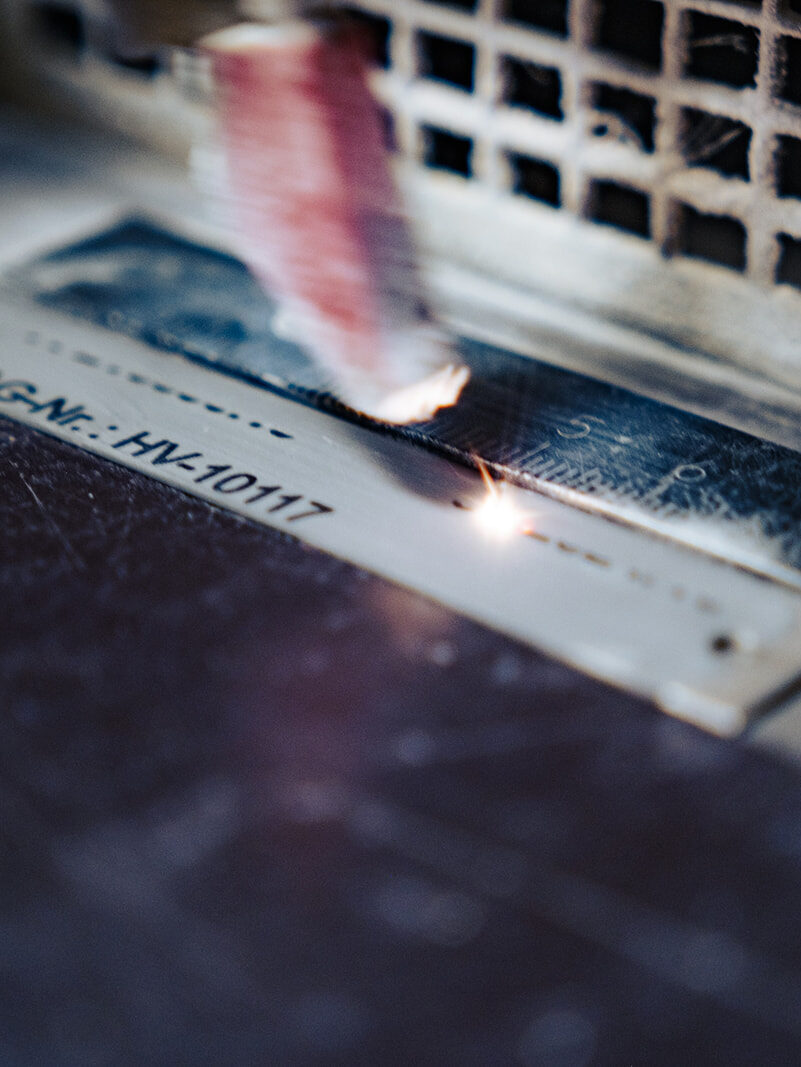
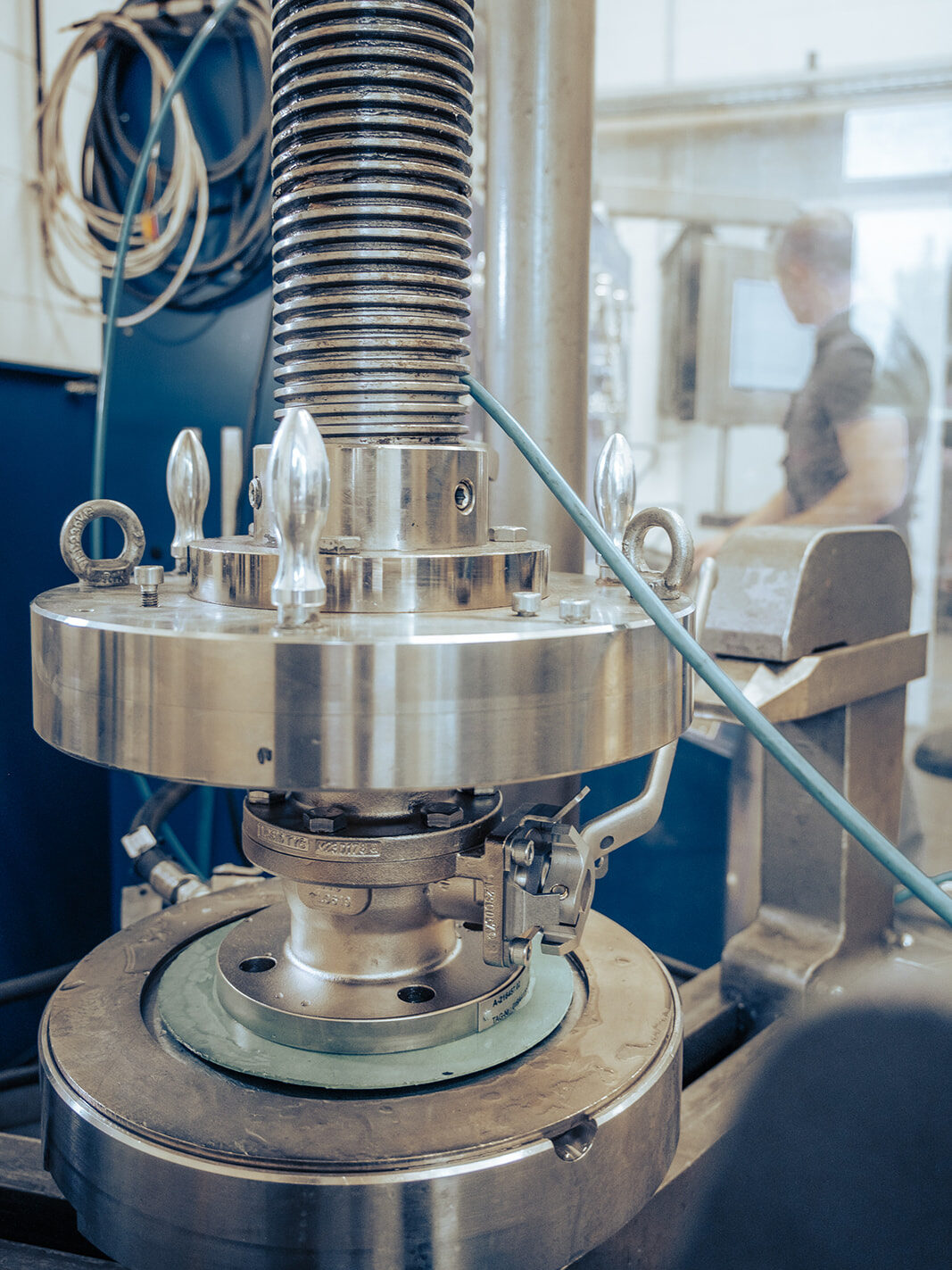
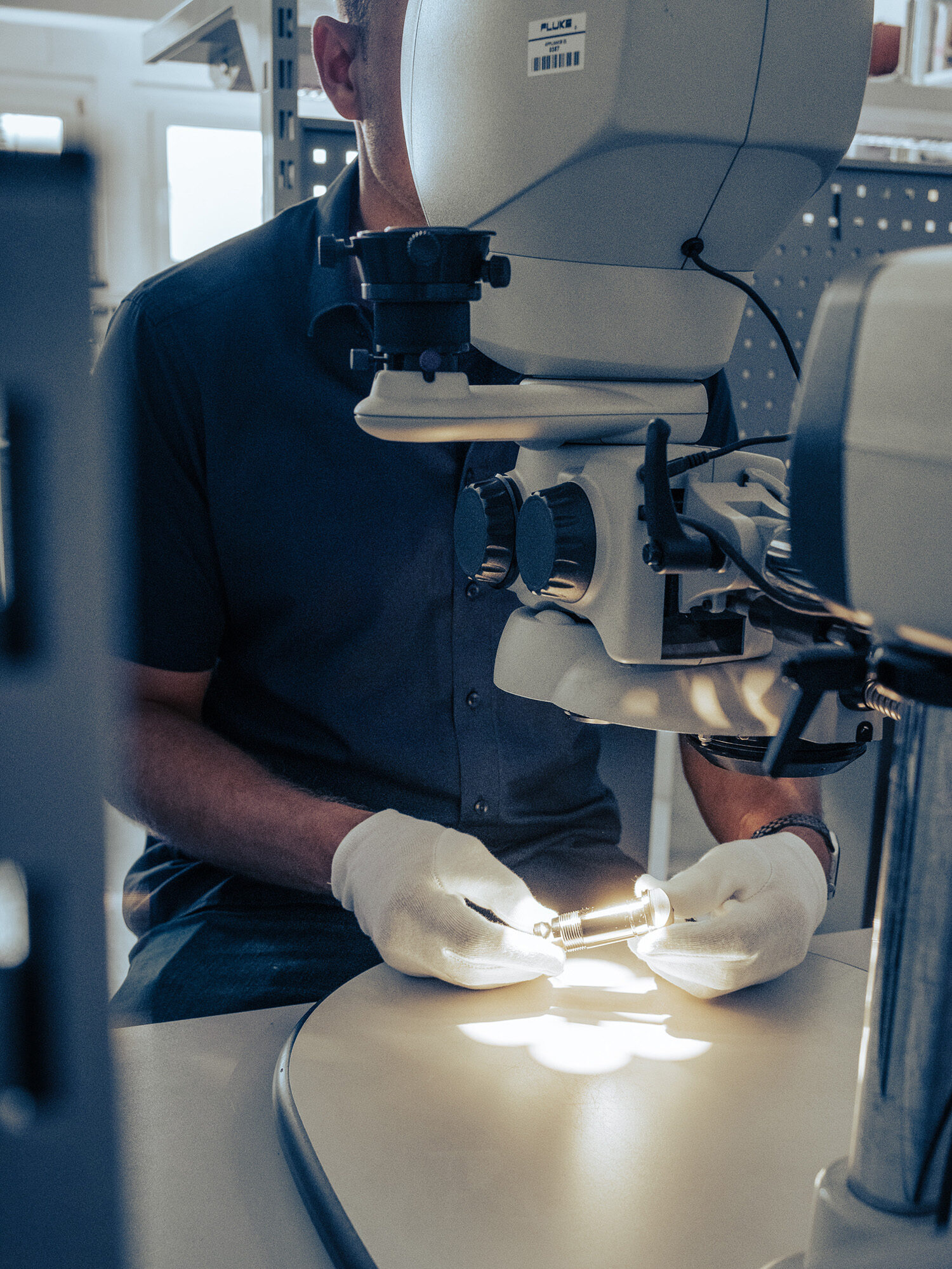
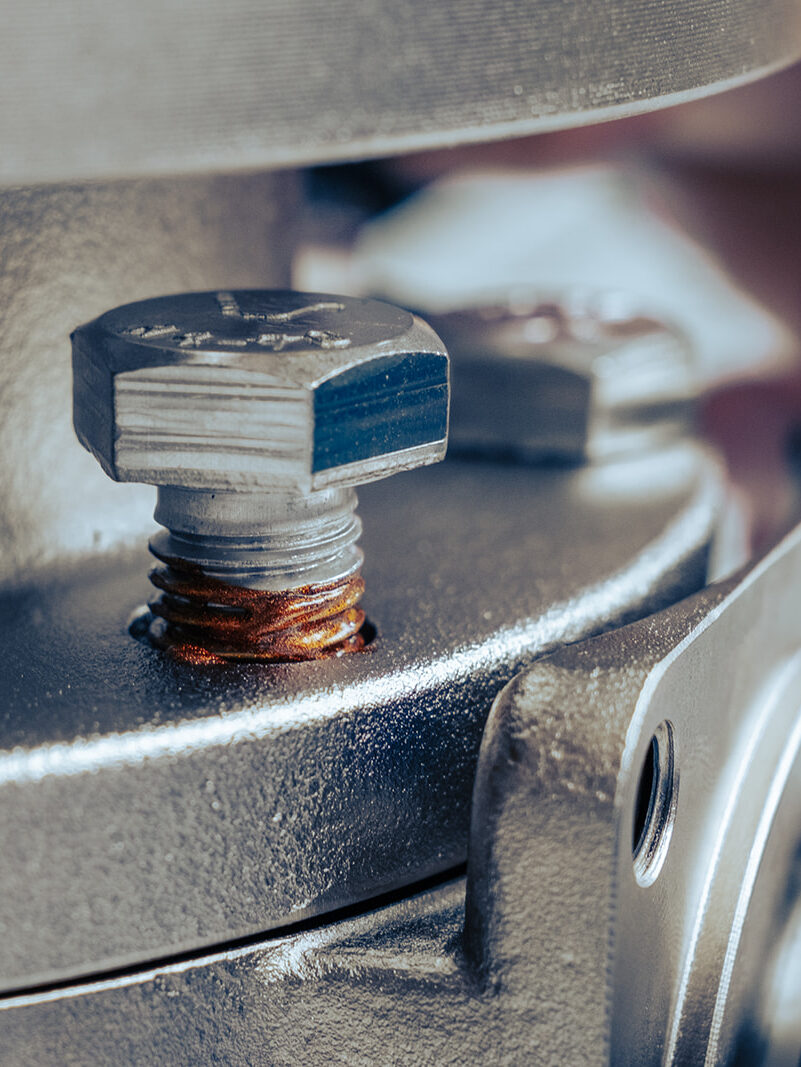
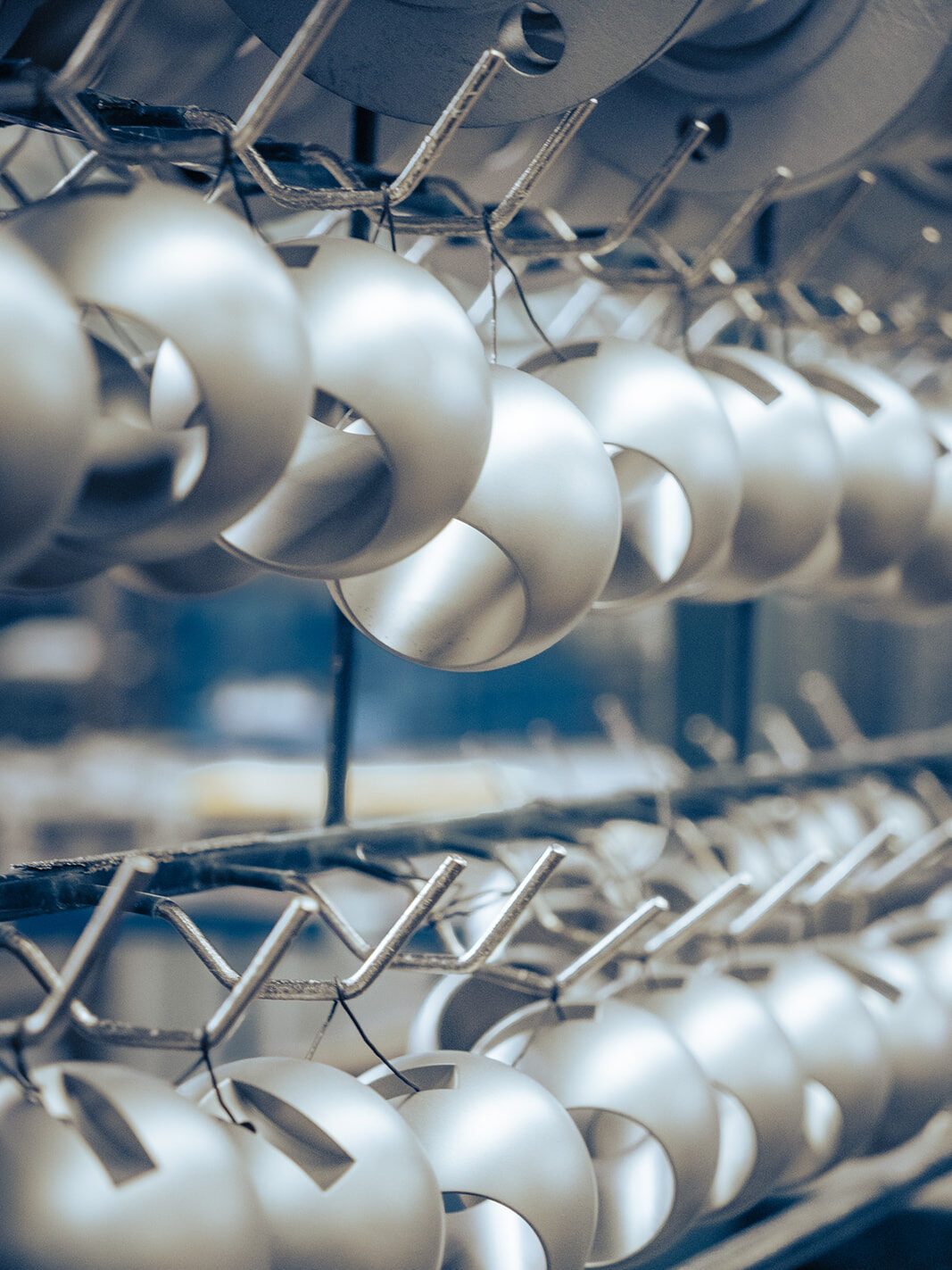
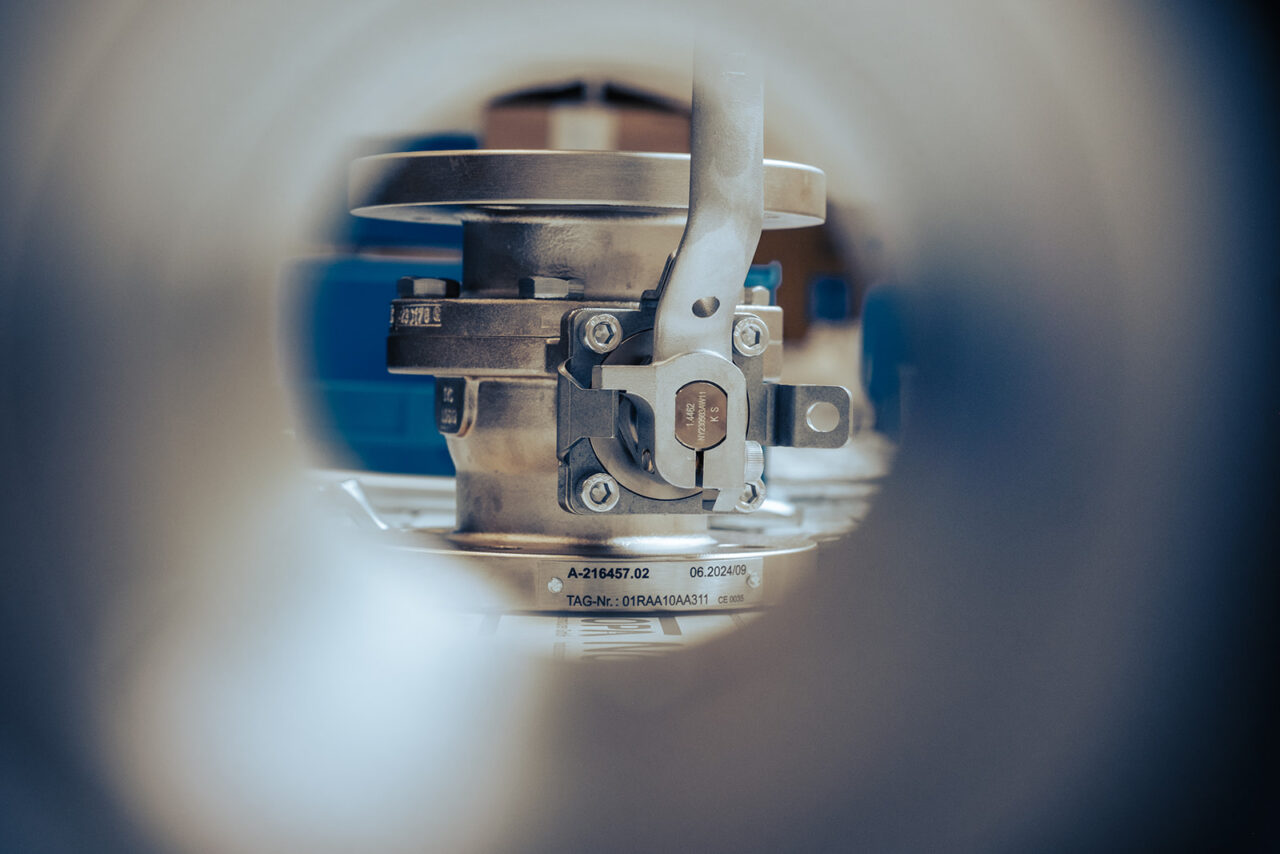
Development of the NOPA-Chem range of fittings
Planning
To meet this challenge, NOPA further developed tried-and-tested valve designs. These were to be made corrosion-resistant to the aggressive potassium hydroxide solution by means of a special nickel coating. In addition, special sealing elements were designed to reliably prevent the potassium hydroxide solution from escaping. The valves had to be designed to ensure that they could withstand the extreme conditions of alkaline electrolysis – temperatures of up to 90 °C and pressures of up to 40 bar.
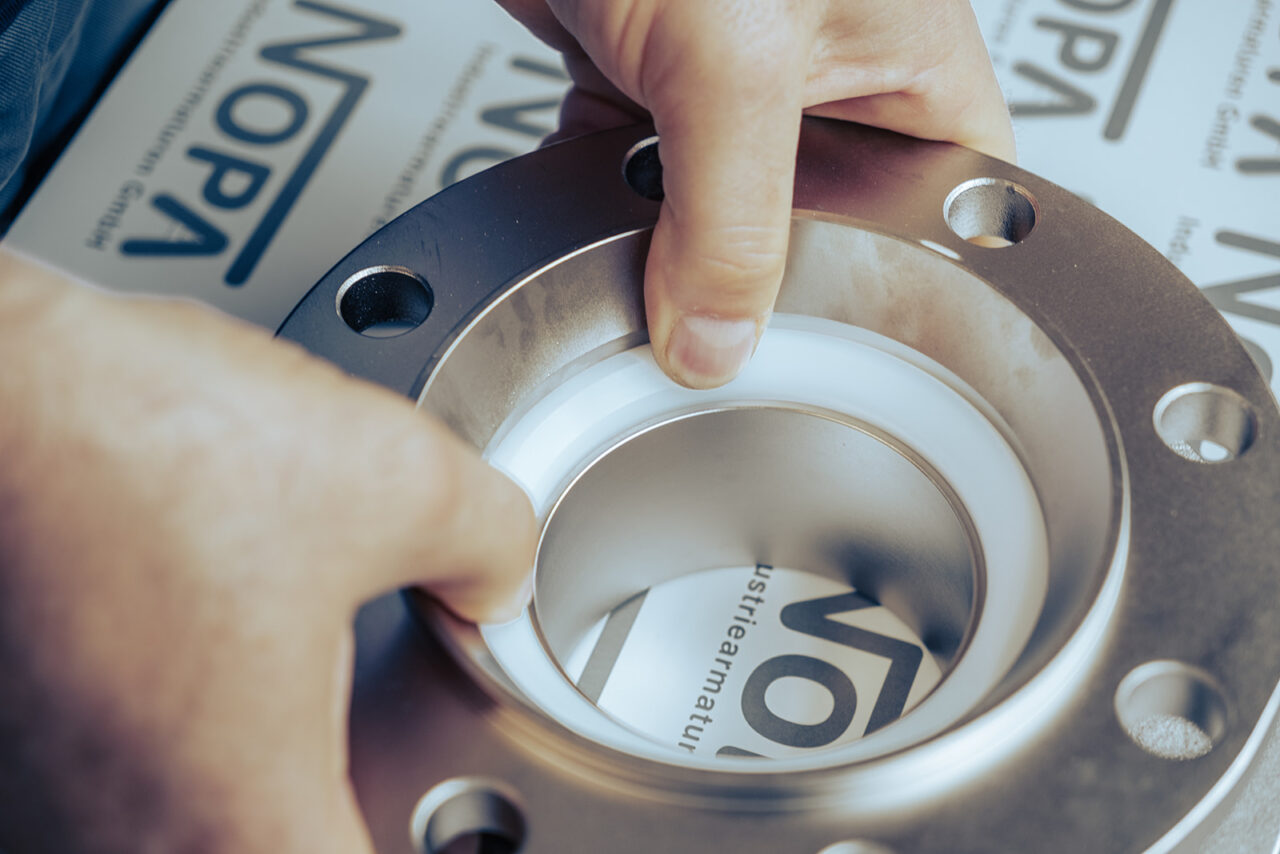
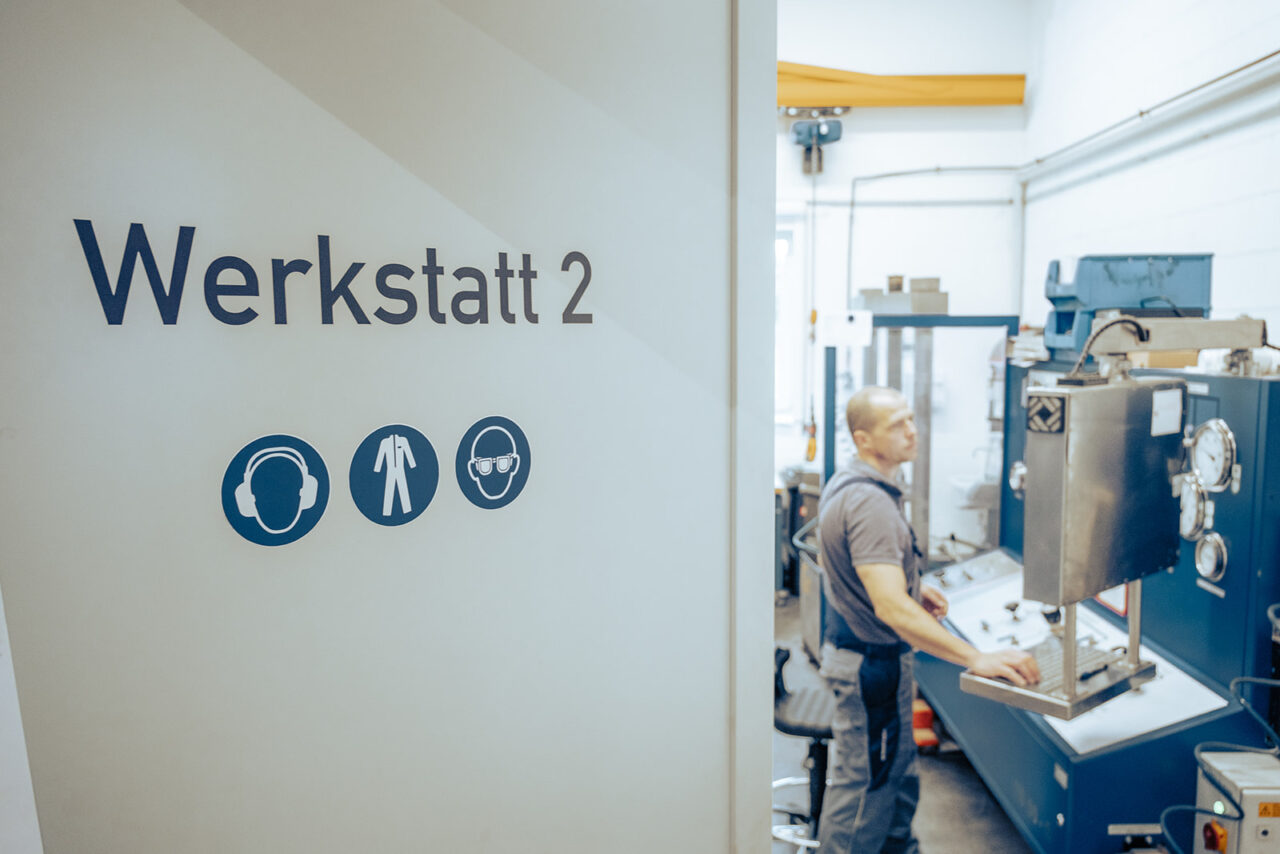
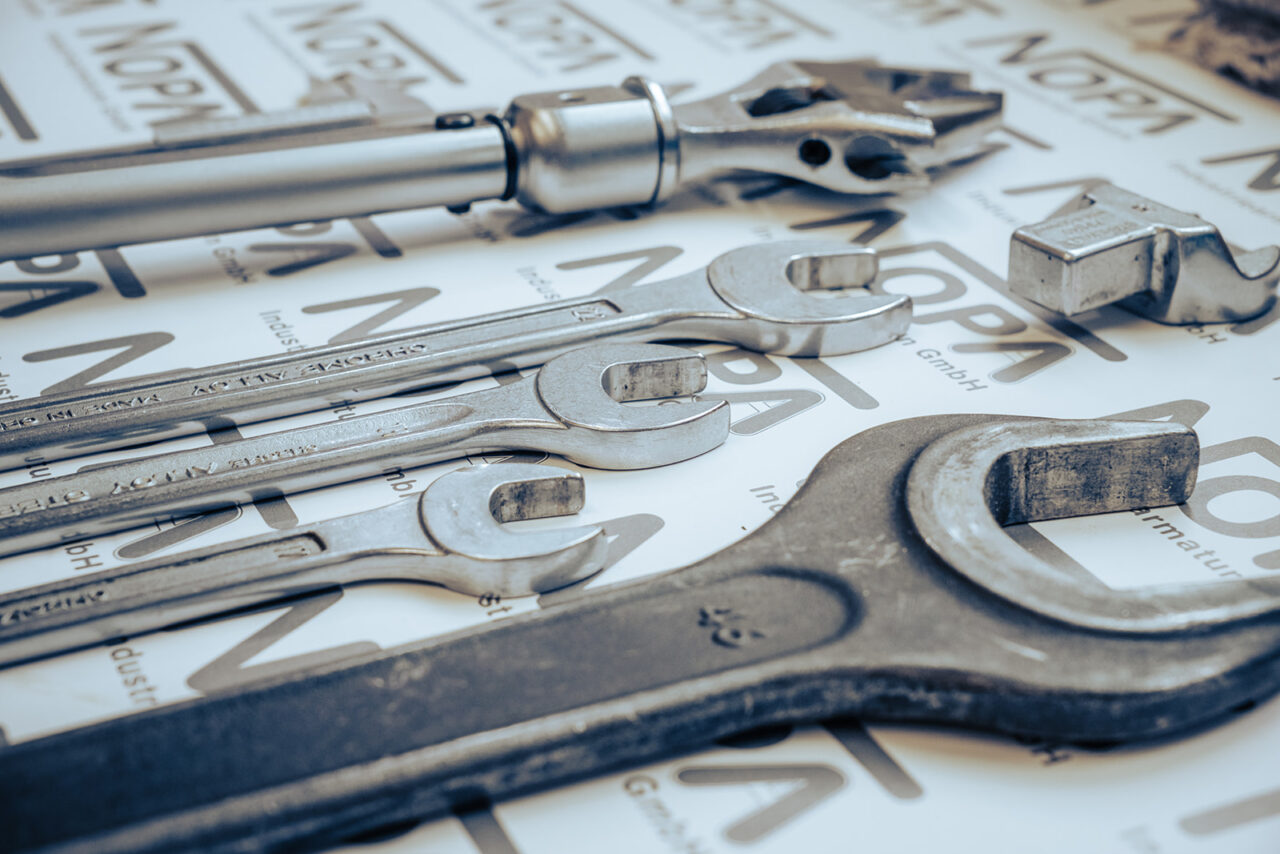

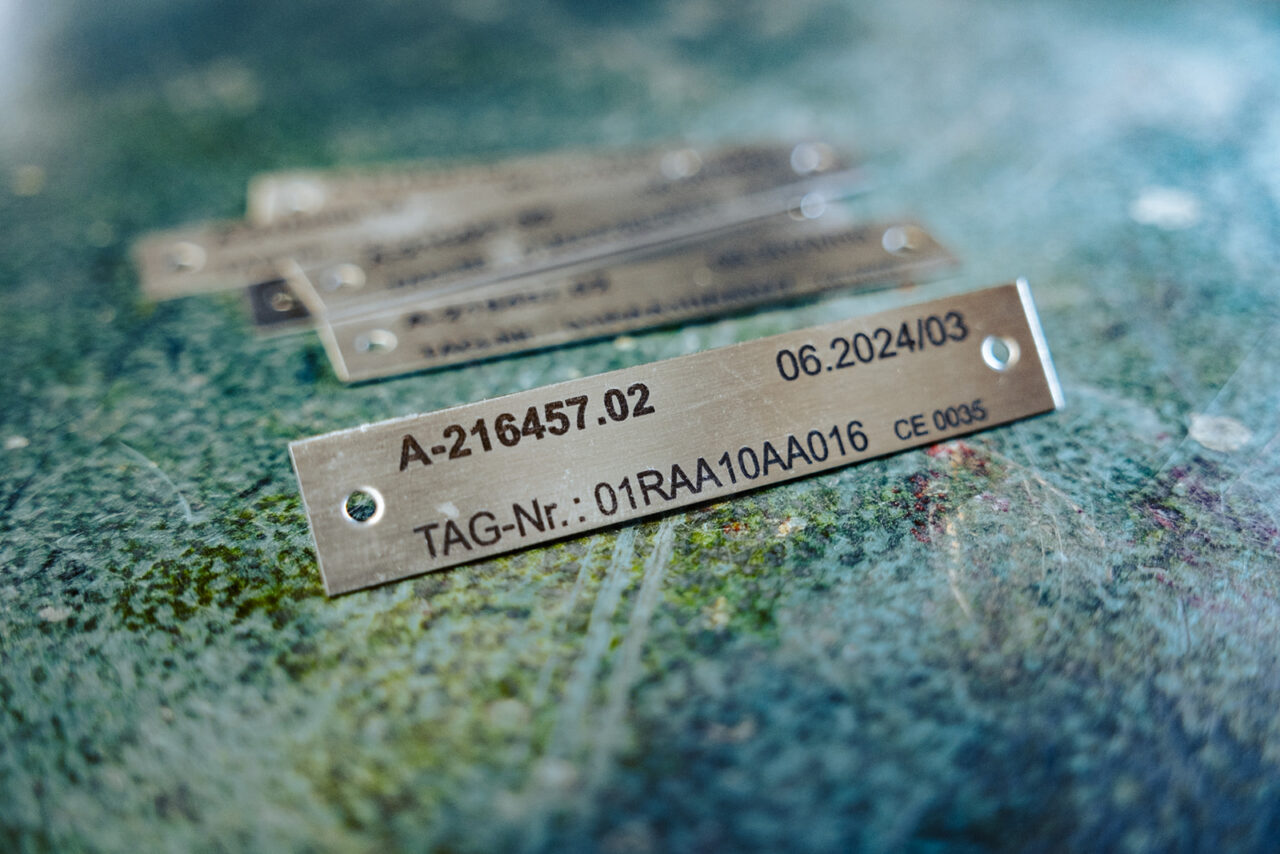
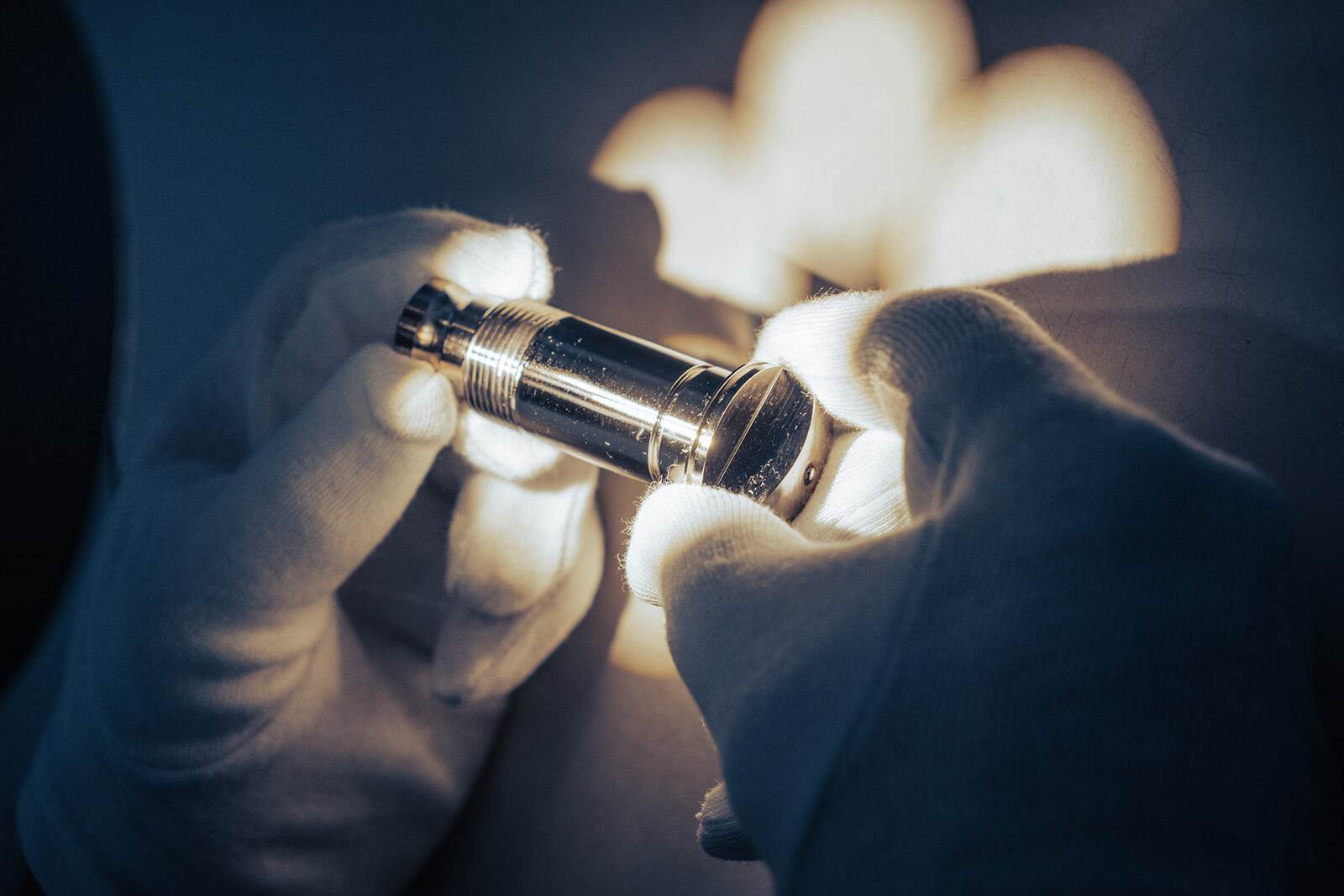
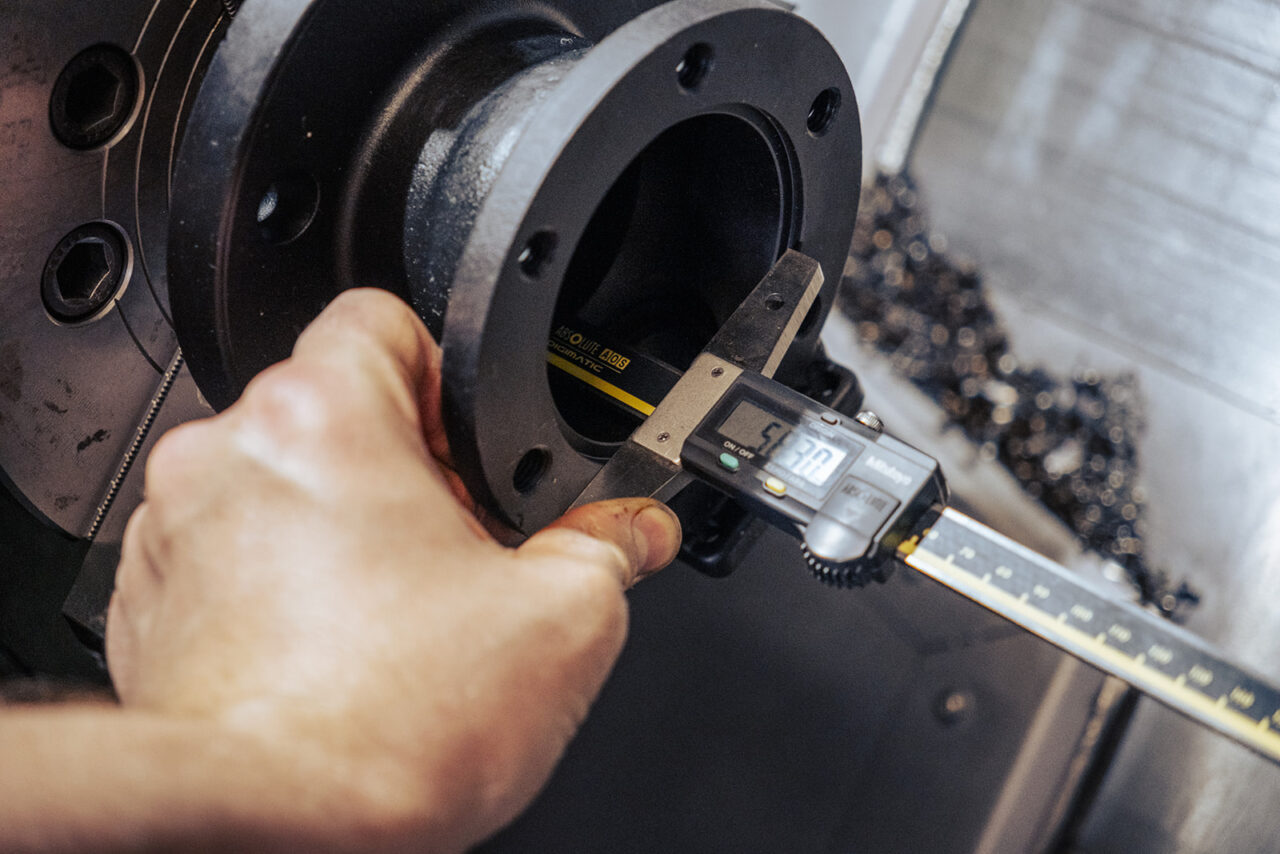
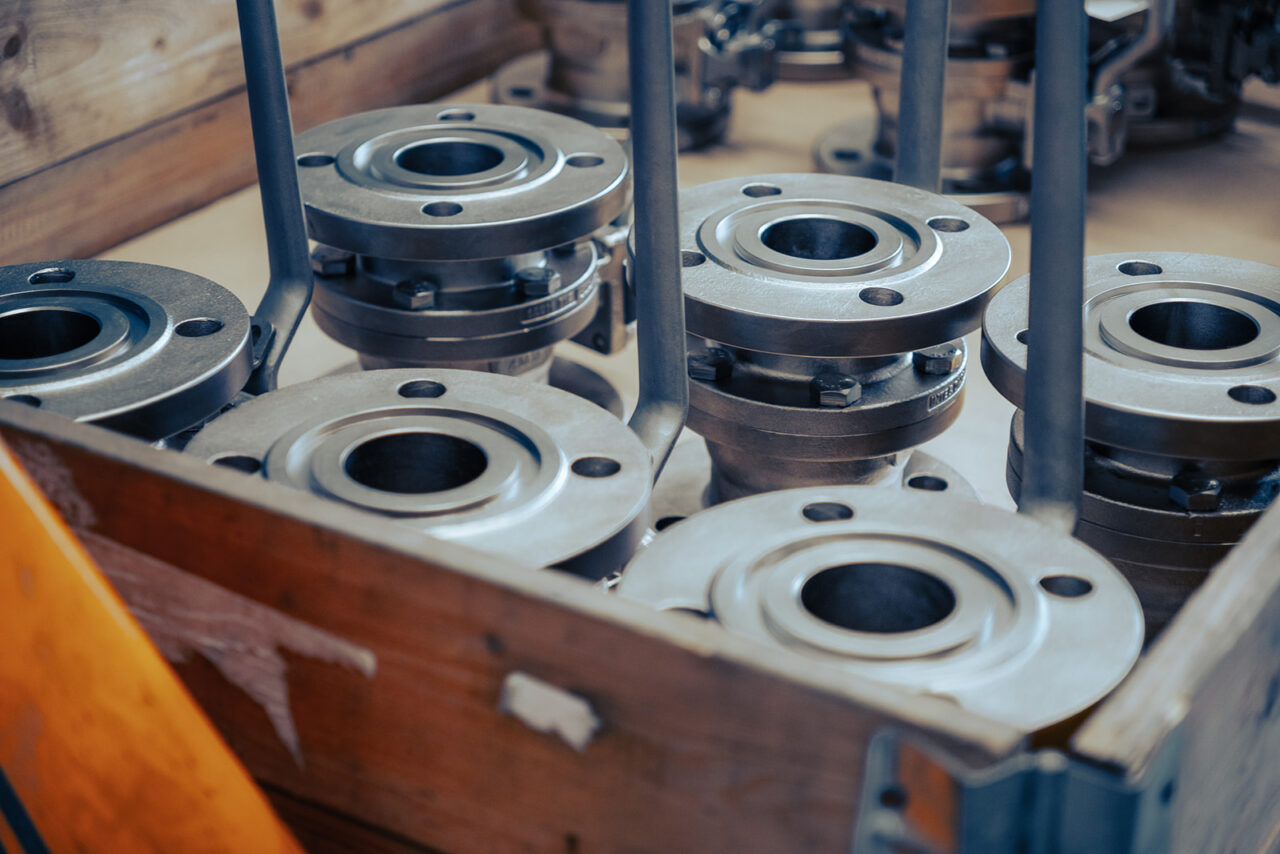
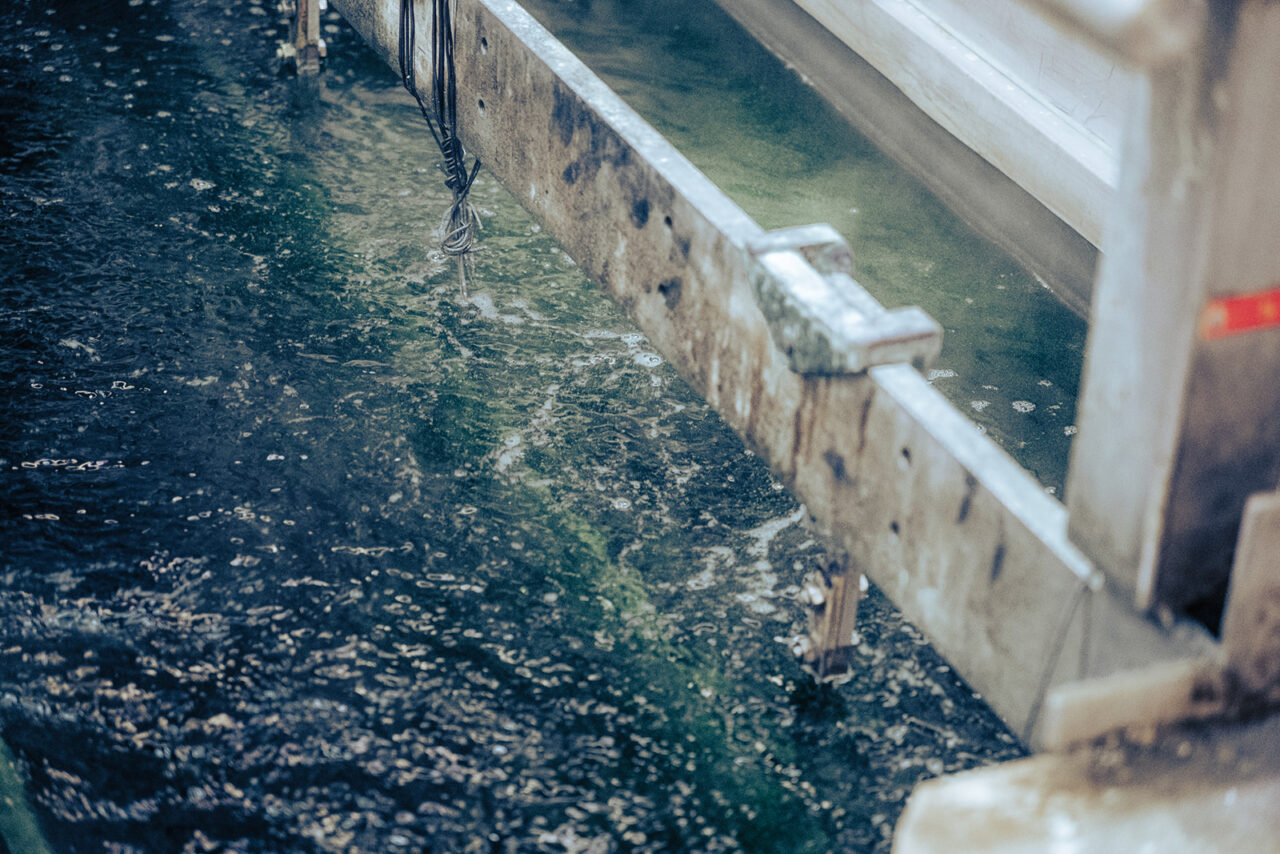
Reliable fittings for extreme conditions
Result
In developing the NOPA-Chem valves, NOPA was able to create a solution that meets the special requirements of alkaline electrolysis. The special nickel coating effectively protects the valves against the corrosive effect of the potassium hydroxide solution, while the sealing elements prevent the alkaline solution from escaping. This ensures that the valves function reliably even under extreme operating conditions. With this project, NOPA has not only solved a technical challenge, but has also taken a significant step from a trading and service company to a valve manufacturer.
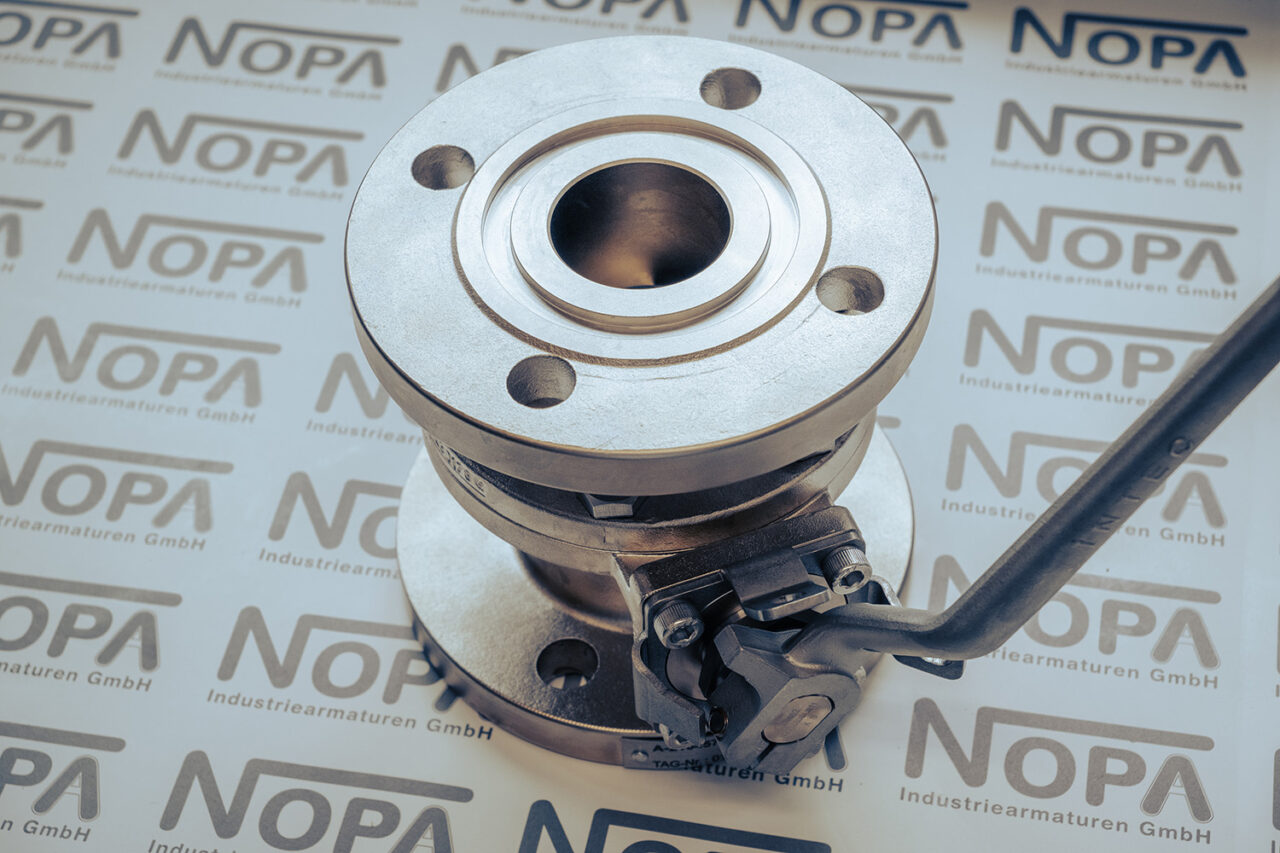
More references from the category
Basic materials
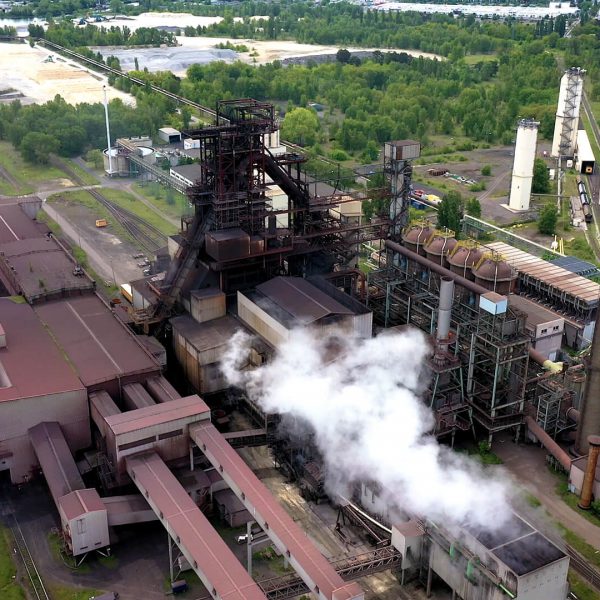
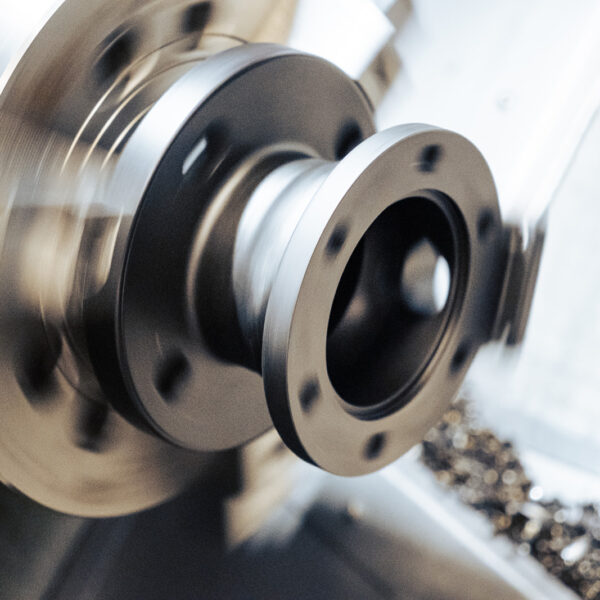
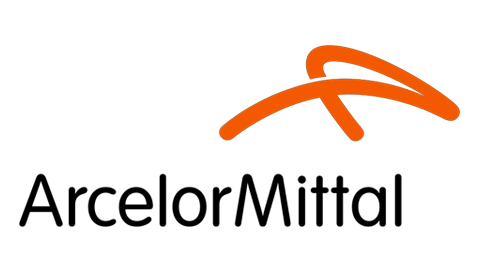
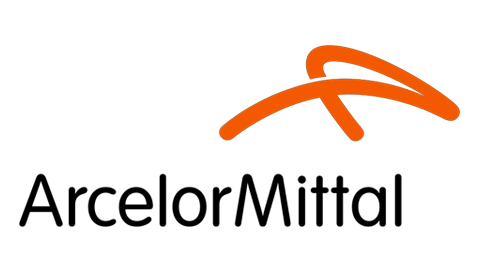
Industry Category | Grundmaterialien |
Project period | 2010 - 2010 |
Client | Arcelor Mittal Eisenhüttenstadt GmbH, ETABO Energietechnik und Anlagenservice GmbH |
Location | Eisenhüttenstadt |
Details | Also involved in this project: Böhmer GmbH, Rudolf von Scheven GmbH Armaturenfabrik & Apparatebau |
Partner | |


Industry Category | Grundmaterialien |
Project period | 2016 - 2017 |
Client | Linde Gas Produktionsgesellschaft mbH & Co. KG |
Location | Eisenhüttenstadt |
Details | Also involved in this project: Ireland S.A. Robinetterie, Industrielle bar GmbH Pneumatische Steuerungssysteme, AUMA Riester GmbH & Co. KG |